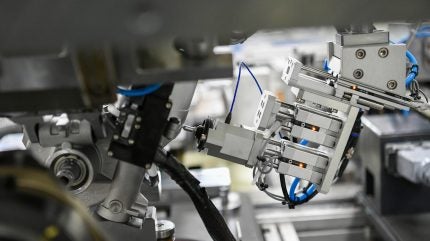
Hyundai Mobis says it has developed an AI system utilising sound for quality inspection, which is now being implemented in its production lines at the Changwon EPS (Electric Power Steering) plant.
The approach leverages artificial intelligence to analyse the ‘subtle sounds’ generated during product inspection to determine quality accuracy.
Hyundai Mobis says acoustic AI represents a new generation of artificial intelligence technology, distinguished from generative AI, which relies on language for Q&A tasks. It remains relatively untested in the manufacturing industry, the company says.
The key to Acoustic AI is developing algorithms that assign meaning to specific sounds and facilitate appropriate judgments. Hyundai Mobis says it has invested significant effort in developing various AI-based technologies over the past few years, now showcasing production technologies specialised in quality control.
Hyundai Mobis plans to extend the Acoustic AI inspection system from the Changwon plant to other component production lines, prioritising parts like braking systems that inherently generate noise due to their operational nature.
Choi Nak-Hyun, Vice President and Head of Digital Transformation at Hyundai Mobis, said: “This initiative marks a pioneering example of process innovation not only in the automotive sector but across the global manufacturing industry. We will continue introducing differentiated AI-based technologies for production, R&D, and improvements in work environments.”
Access the most comprehensive Company Profiles on the market, powered by GlobalData. Save hours of research. Gain competitive edge.

Your download email will arrive shortly
We are confident about the unique quality of our Company Profiles. However, we want you to make the most beneficial decision for your business, so we offer a free sample that you can download by submitting the below form
By GlobalData
While generative AI emphasizes versatility for general users, Acoustic AI is designed for industrial applications, especially smart factories. Its primary advantage is processing large volumes of tasks in a short time. The inspection system at the Changwon plant can detect defective products at a rate of one unit per second.
The Changwon plant produces approximately 1.3 million units of EPS annually. The production process includes 23 stages, from component assembly to vibration and noise inspection.
Since EPS directly impacts steering performance and safety through the steering wheel, meticulous quality checks are essential. Noise inspections are conducted by connecting actual power to the EPS. The sound generated by the rotating motor creates a consistent waveform, which the AI analyzes to identify deviations or anomalies.
Previously, suspect defective products below a certain threshold were initially filtered by an automated system after assembly, followed by manual re-evaluation by specialists. To enhance quality competitiveness, Hyundai Mobis collaborated for about a year with on-site engineers, production technology experts, and AI specialists holding advanced degrees to gather and analyze data, successfully developing Acoustic AI. This system can now distinguish defective products and their causes.
Hyundai Mobis plans to validate and expand the application of Acoustic AI. In the manufacturing sector, the company aims to continuously collect meaningful data through its pioneering Acoustic AI and develop proprietary AI models based on this data. The accuracy of this trained AI is expected to improve further, the company says.