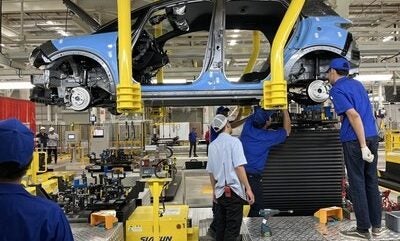
BYD and BMW are two very different auto companies. The former is the Chinese upstart that is tussling with Tesla for the title of world’s leading manufacturer of new energy vehicles, the latter is the venerable 108 year old German company which ranks as the global top selling luxury car brand.
Yet despite their dissimilar pedigrees and target markets, BYD and BMW have made one identical business decision: to make Thailand a base to manufacture electric vehicles and the increasingly sophisticated batteries that power them.
They are far from alone. Thai government tax breaks, subsidies and other incentives are transforming south east Asia’s second largest economy into a global hub for the production of battery electric vehicles (BEVs) and the hybrid technology which is supporting the zero-emission transition.
Even as BYD staged the grand opening on 4 July, 2024 of its THB32bn (US$900m) factory at Rayong in Thailand’s high-tech eastern economic corridor, six other major Chinese BEV manufacturers – Great Wall Motor, Hozon New Energy Automobile, SAIC Motor, Chongqing Changan Automobile, GAC Aion and Chery Automobile – were already either operating or building their own factories nearby.
In addition to this Chinese investment surge, Japan’s Isuzu Motors in March used the Bangkok International Motor Show to unveil the company’s first BEV – a version of the best-selling D-Max one-ton pickup truck – which it said would be built in Thailand and exported to some European markets, such as Norway, starting in 2025. Isuzu, which boasts 50 percent of the Thai pickup market, has filed last year with the Thailand Board of Investment (BOI) a plan to increase its investment in Thailand by THB32bn.
Isuzu’s compatriots, Toyota and Honda, are also embracing the kingdom as a place to advance their own clean energy ambitions by initially focusing on hybrids while taking tentative steps towards EV production.
Access the most comprehensive Company Profiles on the market, powered by GlobalData. Save hours of research. Gain competitive edge.

Your download email will arrive shortly
We are confident about the unique quality of our Company Profiles. However, we want you to make the most beneficial decision for your business, so we offer a free sample that you can download by submitting the below form
By GlobalData
So, too, is Korea’s Hyundai Motor Company. Its unit, Hyundai Mobility Manufacturing (Thailand) received approval from the BOI in August 2024 to invest THB1bn to start in 2026 the local assembly of BEVs and the batteries that power them.
Of the major European investors, Mercedes-Benz has been assembling electric cars and batteries in Thailand since 2022. BMW, which leads the premium market segment and has been building cars in Thailand since 2000, will launch its first locally made EVs in the second half of 2025. In March 2024, it broke ground on a EUR42m fifth generation high voltage battery plant in Rayong.
That same month, Chinese battery maker SVOLT Energy Technology, in partnership with Thai energy company Banpu Next, began producing EV battery packs in Thailand, further evidence the kingdom is not only building vehicles but also creating a localised supply chain to support the sector’s growth.
Then in May, Changan announced partnerships with Thailand parts manufacturers including AAPICO Hitech PCL and Thai Summit Group as part of a total procurement plan worth THB20m ($540m) to produce Changan EVs locally from the start of 2025.
In total, 18 clean energy automakers have invested $2.2bn in the kingdom, a figure the BOI believes could soar by 10-fold by 2027.
“I follow these topics very deeply, but even I was surprised at how the market has developed here in the past year,” Eric Ruge, managing director of BMW Manufacturing (Thailand) said in an interview. “Customers are marching in the direction of battery electric vehicles.”
Thailand has long been a successful player in the conventional internal combustion engine (ICE) auto industry, ranking 10th in the world and number one in Southeast Asia as a manufacturer in 2023.
Now government policies offering subsidies, tax breaks and other incentives to manufacturers and consumers have catapulted it towards the top of the EV rankings, ahead of the U.S. and chasing market leader China.
Even when enthusiasm for BEVs began to falter in other countries, Thailand this year offered “an unwavering commitment” to maintain its consistent support.
That consistency has not only led to a surge in BEV sales locally but also contributed towards what analysts at Bloomberg Green, a unit of the New York-based financial news service that focuses on the business, science and technology of climate change, say will be a tipping point for mass adoption of zero-emission vehicles.
The tipping point, the analysts estimate, is a 5% market share – the level at which new technologies such as smart watches typically start to take the world by storm. So far 31 countries have met that figure for EV sales with Thailand being one that surpassed it “in blazing fashion,” they noted.
In 2023, EV sales in Thailand soared by almost eight-fold to 76,000 accounting for 12% of all vehicles sold. In the first quarter of 2024, the EV market share rose to 14%.
“Thailand emerged as Southeast Asia’s EV pioneer,” Bloomberg Green reported.
And that is just the start. Before this year, almost all EVs sold in Thailand were imported mostly from China. Now with the opening of so many local production facilities, the annual sales figure for 2024 is set to double again to 150,000, a 20% market share of all vehicles produced, the Electric Vehicle Association of Thailand has forecast.
The country’s next big target is a so-called “30@30” strategy that aims for 30% of vehicles manufactured by 2030 to be EVs. These include not only private cars, but also trucks and buses.
Given that more than half of Thailand’s 2.5m vehicle manufacturing capacity will be exported, that would make the kingdom an even more important global contributor to clean energy vehicle production.
“Thailand aims to become a major EV manufacturing hub for domestic and export markets,” the International Energy Agency, a Paris-based intergovernmental organization comprising countries that account for 80% of global energy consumption, said in its 2024 Global EV Outlook. “New subsidies, including for domestic battery manufacturing, and lower import and excise taxes, combined with the growing presence of Chinese carmakers have contributed to rapidly increasing sales.”
The most visible of those Chinese carmakers is BYD, which has chosen Thailand as its first production base outside China.
When it entered the local market in 2022 with an imported model, the Atto 3, Thais queued outside showrooms to buy it. Last year, following the introduction of imported Dolphin and Seal models, BYD sold 30,000 cars locally – a 40% share of the Thai EV market.
It also struck a deal for Bangkok-based Rever Automotive to assemble its battery powered buses and trucks.
Now the opening of its new Rayong factory, with a production capacity of 150,000 vehicles a year, seems destined to play a key role in the company’s swift international expansion especially across the 10-member Association of Southeast Asian Nations (ASEAN), a market of 670m people.
“We already have plans to export into ASEAN countries, the Australian market and even Europe,” Benson Ke Yubin, general manager of BYD Thailand said in an interview.
With so many other potential locations to choose from, what persuaded the Chinese BEV giant to invest in Thailand? Like other manufacturers interviewed for this article, Ke singled out Thailand’s supportive policies and the role of the BOI in assisting investors. “We feel confident investing here,” he said.
If the speed of Thailand’s transition to BEVs sounds ambitious, it is based on a proven strategy. To get where it is today as a global leader in conventional ICE vehicle production, it not only attracted foreign car manufacturers, but also developed a sophisticated onshore supply chain of parts makers.
Now a prime objective is to attract investment in the manufacturing of battery cells to complete the localisation of the most important parts of the EV supply chain.
But how did Thailand persuade car and battery makers to move so swiftly? Several years ago, the government identified “the car of the future” as one of five key strategic new technology industries it aimed to develop.
Then in 2022 the incentives it offered foreign EV producers included allowing them to import vehicles for the first two years on condition they agreed to build factories soon after.
Those companies that begin local production by the end of 2024 get the most privileges, although automakers opening factories between 2025 and 2027 will continue to be incentivised.
The result has been the surge of investment followed by a jump in EV production as the new local factories come online.
First off the blocks was Great Wall Motor, which in 2020 acquired a conventional auto factory from General Motors, then announced it would spend THB22.6bn ($615m) converting it to manufacture hybrids and EVs. The first hybrids rolled off the production line in June 2021 followed by EVs in January 2024.
Capable of producing 80,000 vehicles a year, including the Ora Good Cat, Haval and Tank models, the company describes the Rayong factory as its key production base for right hand drive vehicles in south east Asia.
Then in March, Hozon fully opened what it termed “the first 100 percent EV factory in Thailand”, producing the Neta V small car which in Thailand competes in price with similar ICE models.
Even before local manufacturing began, the Neta V had become an established favorite in Thailand following Hozon’s launch of the imported model in 2022. Within a year, 14,000 Netas had been sold, catapulting it to number two EV brand and into the top 10 best selling car models of all types in that year. “We took just one year and one model to gain consumer acceptance in Thailand,” Neta Auto (Thailand) General Manager Shu Gangzhi said in an interview. “This gave us confidence to invest more in this market and that’s why we decided to start production here.”
Now, with a production capacity of 30,000 annually, the company is looking beyond Thailand’s borders. “We are also preparing the basis for exports to other Asian markets and maybe other markets such as South Africa, for both left and right hand drive vehicles,” Shu said.
Why did Hozon choose Thailand? “It has the most attractive, stable EV policy – very realistic – with incentives for both consumers and manufacturers,” Shu added. “It is also a large and sophisticated market.”
Both Great Wall and Hozon use batteries supplied by the new SVOLT JV factory. While SVOLT was originally the battery unit of Great Wall Motor Holdings, it now gets 70% of its business from other manufacturers, SVOLT’s senior vice president, Feng Zhang, said.
He added part of SVOLT’s decision to choose Thailand for its first factory in south east Asia stemmed from its earlier experience. “Progress has been fast and smooth and this gave us very high confidence,” he says.
The bottom line, however, was commercial. “We are doing our business independently,” Zhang adds. “We expect a very high EV transformation in Thailand. In China, the EV market share is close to 50%. I think the same will happen in Thailand. This is going to be a huge market for us.”
Back at BMW’s factory in Rayong, managing director Ruge doesn’t attribute Thailand’s success at winning investment entirely to its incentives or market opportunities. He also gives high praise to the Thai workforce.
Of BMW Group’s global production network comprising 30 manufacturing plants in 15 countries, Rayong is unique in that it builds both cars and motorcycles under the same roof.
“It’s a small plant, but it’s extremely complex,” Ruge says. “And it’s absolutely impressive how they can build these cars and motorcycles without any compromise in quality. I have worked all over the world, but what I have experienced here is really exceptional.”