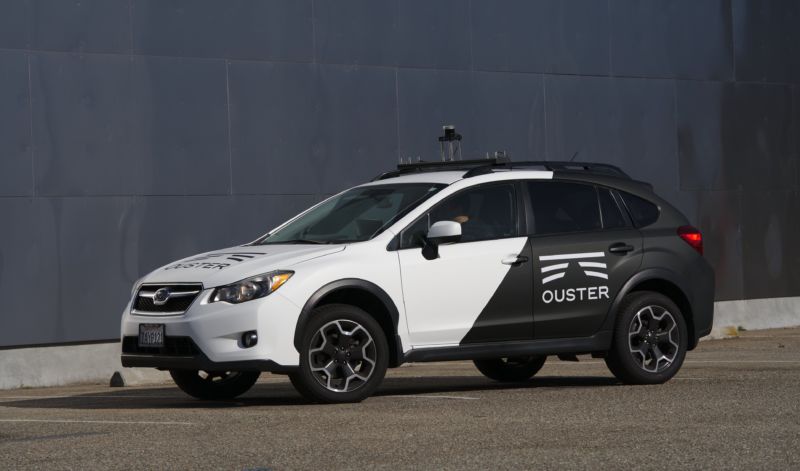
Dozens of startups are working on lidar, a type of laser sensor that many experts see as essential for fully self-driving cars. In my view, one of the most interesting companies is called Ouster. I first wrote about Ouster back in May, when I explained how it was bucking an industry trend toward fixed “solid state” lidar in favor of the spinning design pioneered by industry leader Velodyne.
Because Ouster’s lidar looks so much like Velodyne’s on the outside, I assumed that it looked similar inside, too. But in a recent interview with Ars Technica, Ouster CEO and co-founder Angus Pacala told me that Ouster’s lidar is actually radically different inside.
Patent filings show that Velodyne’s venerable 64-laser lidar has a stack of circuit boards, each connected to an individually packaged laser. By contrast, if you crack open the case of Ouster’s 64-laser unit, you’ll find that all of its 64 laser beams emanate from an integrated circuit not much bigger than a grain of rice.
Ouster’s decision to initially focus on a conventional spinning lidar unit may turn out to be a bit of a head fake. Ouster started with a Velodyne-style spinning lidar partly because potential customers are familiar with the design and partly because the spinning design works with relatively few lasers—16 or 64 in Ouster’s initial designs. But Ouster’s longer-term vision is to pack many more lasers into an integrated circuit—thousands of lasers, and perhaps eventually millions. And that could enable the creation of a new type of solid-state lidar that offers compelling advantages over the solid-state lidars on the market today.
For this story, Ouster gave Ars an exclusive in-depth look at the technologies underlying its lidar units. As far as I know—and I’ve talked to a number of people in the industry—Ouster’s lidar is unlike any others on the market today. It’s built on semiconductor chip technologies that have the potential to improve over time in much the same way that digital cameras did 15 years ago.
“People are going to be surprised how fast our technology improves,” Pacala told me.
That’s significant because cheaper, better lidar is a key hurdle for mainstream adoption of self-driving cars. Lidar suitable for self-driving cars today costs thousands—if not tens of thousands—of dollars for a single sensor. Ouster is laying the groundwork to change that.
The challenge of solid-state lidar
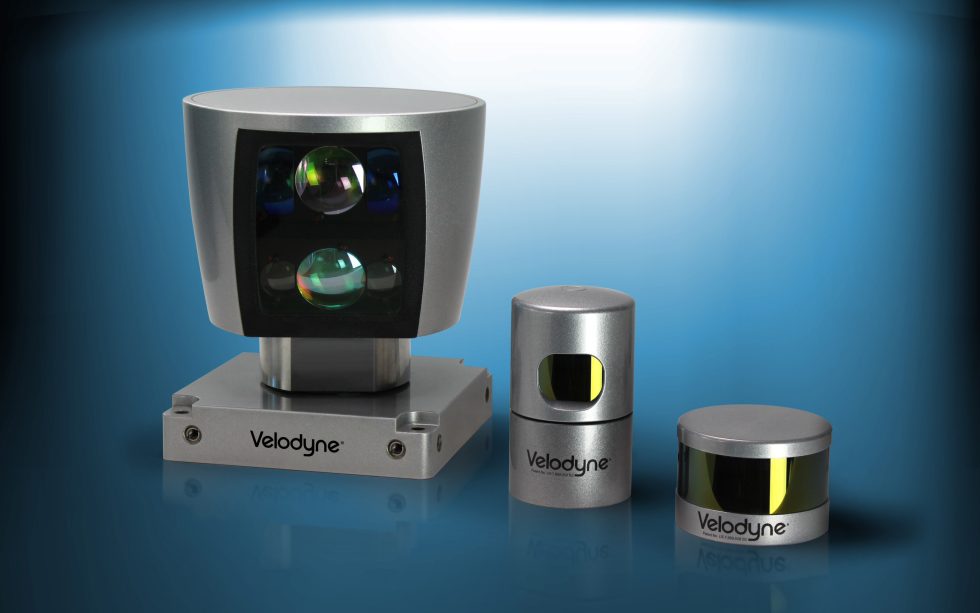
Until Velodyne founder David Hall came along in the mid-2000s, lidar sensors were two-dimensional: they scanned a single horizontal slice of the world. Hall realized that he could greatly improve on this design by basically stacking 64 of these horizontal range-finders on top of each other, producing a three-dimensional point cloud with a vertical “resolution” of 64 points.
While the concept was simple, actually manufacturing a Velodyne-style lidar is fiendishly difficult. Each laser needs to be precisely aligned with a corresponding detector, and the whole system needs to stay well-aligned as it spins around—and as the car it’s attached to bounces over potholes. The complexity of getting all this to work helps to explain why Velodyne’s high-end units have historically cost about $75,000.
An obvious strategy for building cheaper, more durable lidar is to try to pack most of the components into an integrated circuit—after all, that’s how we got from room-sized computers to ones that fit in our pockets. Over the last five years, we’ve seen a number of companies try to develop “solid state” lidars that do that. All of these lidars dispense with the spinning head in favor of a fixed sensor unit that’s permanently pointed in one direction.
Up until now, most companies making solid-state lidar have tried one of three approaches:
- In the “MEMS” approach, a single laser beam is “steered” by a tiny mirror. The mirror is small enough (and hence has low enough angular inertia) that it can complete a full two-dimensional scan in a fraction of a second.
- In the flash-lidar approach, a wide-angle laser illuminates the lidar’s entire field of view in one flash. Then an array of sensors detects return flashes from different directions.
- A third approach uses optical phased arrays, a technique for all-electric beam steering.
What all of these techniques have in common is that they replace Velodyne’s 64 lasers with a single laser that illuminates the entire scene—either all at once or with some kind of scanning motion. Conventional lasers are expensive and bulky, so reducing the number of lasers from 64 to one seems like a sensible way to cut costs. But as we’ll discuss more below, these techniques have significant downsides.
Arrays of lasers, locked in silicon

What if, instead, you could put a lot of lasers onto a single chip? This not only brings down the cost per laser, it also eliminates the need for laborious laser alignment during final assembly, since lasers come pre-aligned.
The problem is that the most popular semiconductor-based laser technology, called edge-emitter diode lasers, isn’t really suitable for packing a bunch of lasers together. Edge emitters emit light in the plane of the wafer—which means the wafer needs to be cut open to expose the laser’s emission surface.
“It’s incredibly expensive to build an array out of side-emitter diode lasers,” Pacala said. So these lasers tend to be packaged as individual units.
Ouster uses a different technology called vertical-cavity surface-emitting lasers (VCSEL). VCSELs are not a new technology—they’ve long been used in optical networks, computer mice, and more recently in the auto-focus features of smartphone cameras. But Ouster is one of the few companies to build lidar units with VCSELs—and the only such company we know of with a shipping product and published specs and prices.
As the name suggests, surface-emitting lasers emit light perpendicular to the surface of the wafer. That means there’s no need to cut the wafer in any particular spot for the laser to be functional. And that, in turn, makes building dense arrays of VCSELs much easier.
“The VCSEL die in our laser truly is the size of a grain of rice,” Pacala told Ars. “It’s producing all of the light that our sensors use to see out to hundreds of meters.”
And Pacala says this 64-laser chip is just the beginning.
“It’s just like digital cameras getting higher and higher megapixel counts,” he told us. “Your camera did not change in size or cost, but [designers] were able to pack more pixels in the same space. The exact same thing is happening with us. We’re going to be able to double, quadruple, 10x the resolution, without any change.”
Initially, that will likely mean increasing the vertical resolution of Ouster’s lidar unit. Velodyne’s top-of-the-line unit has 128 lasers—and hence a vertical resolution of 128 points. If all goes according to plan, we can expect Ouster to start one-upping Velodyne by offering spinning lidars with higher vertical resolutions—perhaps 256, 512, or 1,024 scanning rows—without a significant increase in prices.