by the Arrival Materials Team
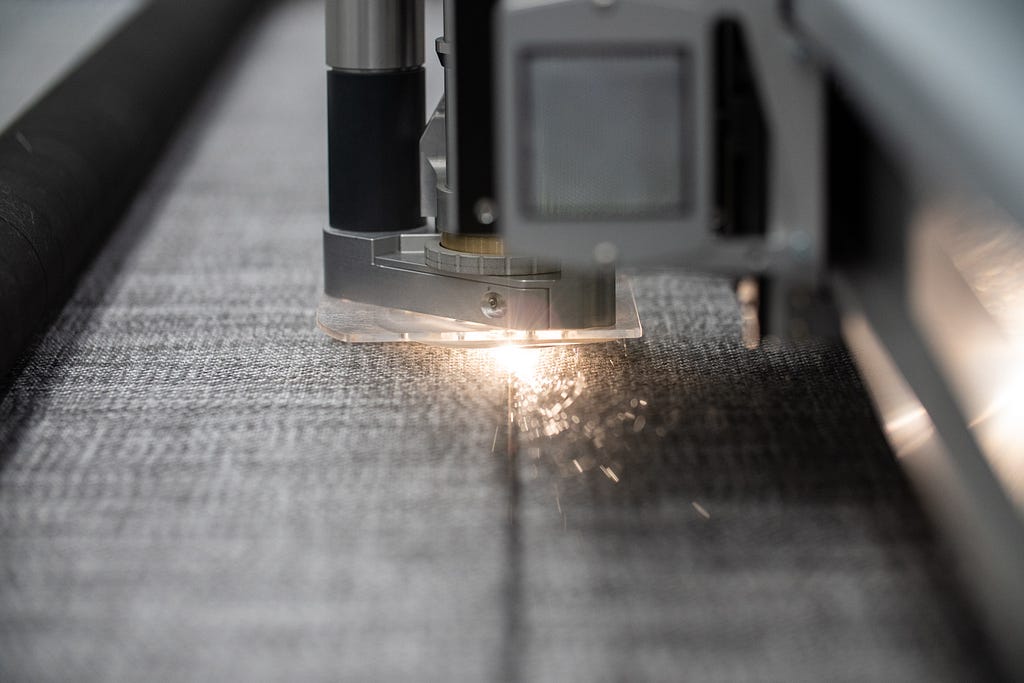
The question is simple: with our knowledge of material technology, how would we design vehicles to be lighter, less expensive, more durable and fully recyclable?
At Arrival we have the freedom to develop completely new ways of thinking about materials for design. This approach has provided engineers with the means to do things differently, which is fundamental if we are to succeed in bringing about a revolution in sustainable transportation. From nano to macro, we have developed a rich and rewarding material palette for Arrival products. There is no need to compromise on quality: our materials are versatile, sustainable and low-cost.
Conventional metal body vehicles are produced from stamped steel or aluminium. Stamping requires huge matched-steel tools (moulds used to press sheet metal into shape); often several pairs are required for a single part in a process known as progressive stamping. This is why it costs tens of millions to set up production — and takes many months to tune the line — more than an entire Arrival Microfactory. To pay back the investment, metal stamping lines are dedicated to a single product for many years. Overcoming this limitation means we can change our designs rapidly and scale our Microfactores to meet local demand.
Once complete, the stamped metal body is welded together to form the familiar body in white (BIW). The welding jigs and robots are dedicated to a single product; further increasing time and investment. Next, metal has to be protected from the atmosphere. This requires a large paint setup, starting with an e-coating line, which may be the most significant investment in the paint shop due to the size of the tanks required to fully submerge the BIW. Subsequent paint layers are built up on top to produce the finished vehicle.
Zero Waste
Arrival is doing things differently. Through an integrated approach to engineering, Robofacturing and material development, we have been able to take a radical new approach to vehicle materials. It starts with the goal of zero waste: we took the opportunity to rethink how we use and consume materials in production and throughout the lifecycle of the things we make. Every specification is driven by a desire to run factories that have a light touch, are a pleasure to go to work in, do not produce harmful emissions or waste; and everything can be reused.
In place of metal bodywork, we have selected thermoplastic composite material. A combination of high-strength reinforcement and polymer matrix, it can be shaped and reshaped many times. We believe in using manmade materials — from recycled sources where possible — engineered to precise tolerances. With small improvements in the chemistry we make materials that are designed to be reused and recycled many times. At every step of production and use, we are ensuring that a recycling loop exists. With every loop, we offset the negative impacts of mining and manufacturing raw materials.
Using an in-house-developed moulding process we call ‘multiform’, we produce finished parts straight from the tool — including high-gloss, textured and textile-covered — so there is no need for a paint shop or costly finishing and laminating processes. And the colour is throughout, which means that minor scratches and damage are not visible; greatly reducing the cost of repairs and replacement.
Light, Strong, Designed
The demands on weight and cost mean that every material we put into the vehicle has to perform several functions. It must be lightweight, to increase payload and reduce demand on energy source; durable to provide long term endurance and minimise the cost and impacts of replacement parts; beautifully executed to present a future vision we all want to be a part of; scaleable, so the designers and engineers are inspired to play, prototype with, and seamlessly transfer ideas to full-production; and low-cost, because we must be competitive to succeed. We know that our future vehicles need to be electric. Right now, the barriers to switching to clean energy are too high; and the highest barrier of all is cost.
The multiform process uses material that is easy to form — this makes automation easier and enables a low pressure process that reduces the equipment and tooling costs. Our proprietary composite material is brought together as layers; each one providing the necessary performance required, such as strength, resistance to ultraviolet light and scratch durability. This approach allows us to build optimised structures tailored to the application, putting strength and endurance where they are needed most. At the end of its useful life, recycling converts all these properties into a single, versatile material.
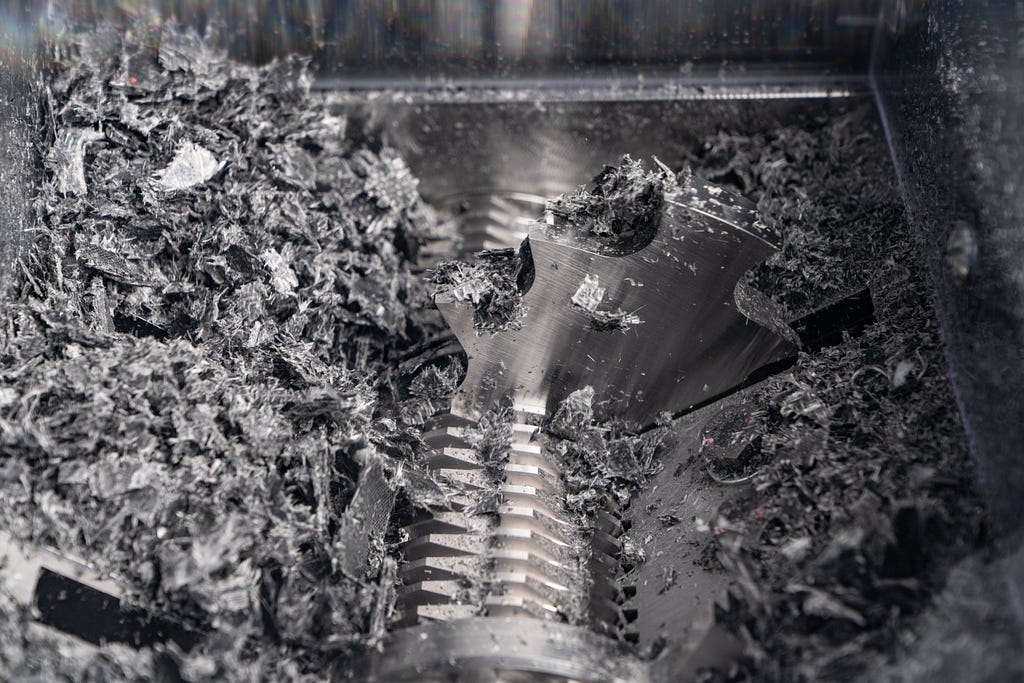
All of these materials are available for the designers to utilise during prototyping. Our multiform process allows for parts to be converted from design to physical sample in less than two weeks, which allows us to rapidly design and develop concepts to production readiness. This is in stark contrast to the typical three to six month lead time for developing metallic parts for the same applications. We aim to reduce this further still, to less than a week, by using 3D printing technology to manufacture recyclable moulds. Our first 3D printing robotic cell is newly operational and we are in the process of validating the first parts.
During the development of our vehicles, we have evolved a versatile palette of materials that bring together these elements of performance and design. In addition to thermoplastic composite, we use lightweight aluminium alloy in the chassis and structural parts, load-bearing sandwich panels to span large flat areas such as floors, and glazing to maximise natural light and visibility.
Robofactory
Our material developments support a fundamentally new approach to manufacturing: building things autonomously at low and high volumes, with robots. We do not require heavy presses, such as used for metal stamping. Instead, we use grippers, vacuum, lasers and other robot-mounted hardware. Things must be easy to handle and fabricate, without the need for human intervention. This allows us to be flexible in our approach to production, deploying factories close to where the products will be used, and in only a matter of months.
We are building things from the ground up. In many cases, this means we have to start from scratch to define the processes and tools. Arrival’s Microfactory equipment uses many of the materials and technologies deployed in our vehicles; albeit tweaked to fit the application. Knowledge transfer means we can make things more quickly and at a lower price point than would otherwise be possible. This is core to how we work: use and reuse the great assets that we have; and never take anything for granted, because you can always find a better way to do something.
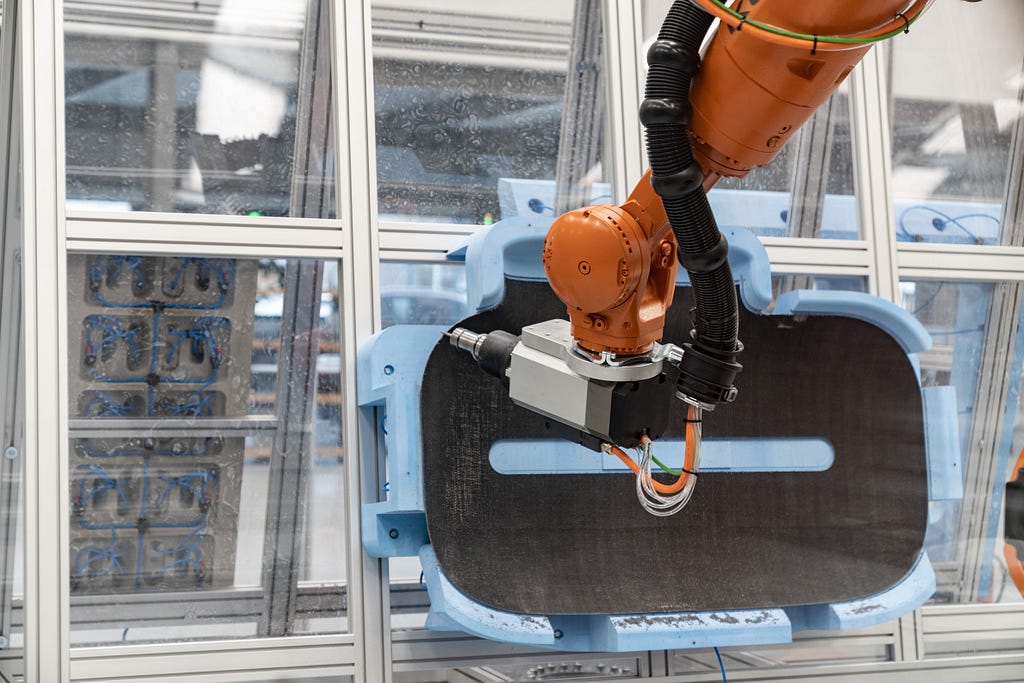
The Art and Science of Materials
In the pursuit of radical performance at low cost, we have moved progressively up the supply chain. Not only do we produce the vehicle; but in the case of our composites we manufacture the panels, the fabrics and the fibres. This creates the opportunity to make improvements at every step, and take advantage of trade-offs that would otherwise not be possible. For example, by adjusting the chemistry of the composite we can improve the efficiency of our moulding cycle, and reduce cycle time and factory cost.
Every material that goes onto our vehicles — composite, aluminium alloy, structural sandwich panel, high-performance adhesive and glass — is meticulously deconstructed and evaluated. They are crafted into reliable and robust substrates, with carefully executed surface and finish. From their bulk properties through micron-thick surface layers, teams of engineers study our materials to ensure that we can achieve maximum performance and efficiency in line with the design team’s aspirations.
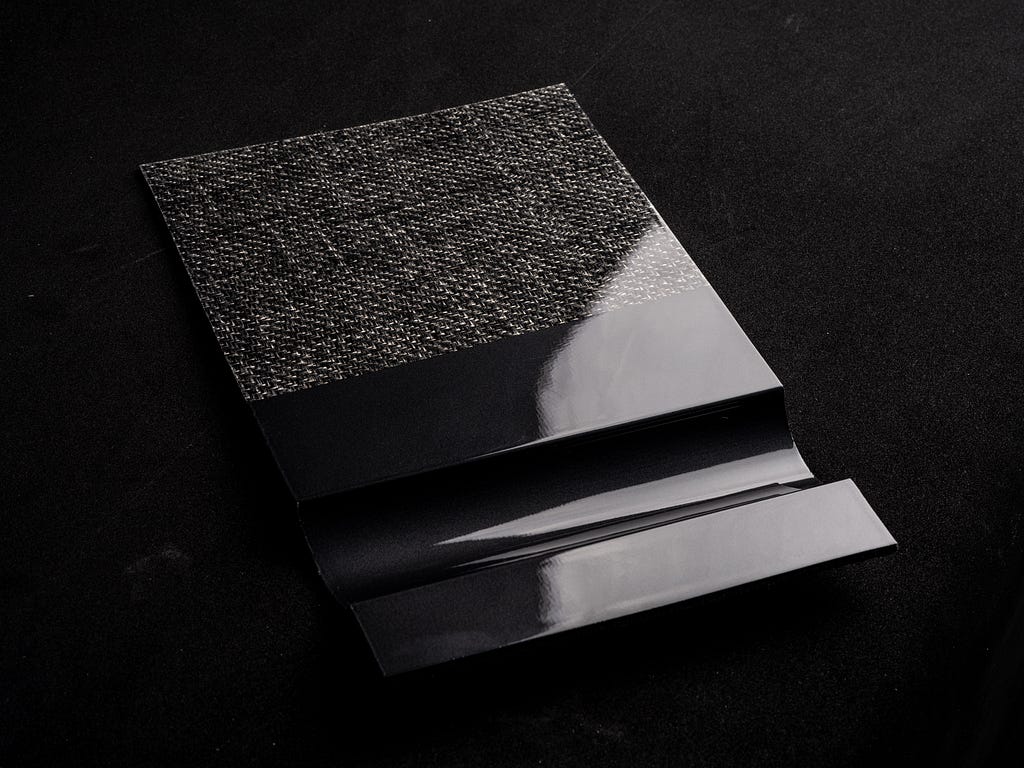
Our composite materials do not behave like conventional automotive body systems. They are 50% lighter than steel and more durable; exterior parts do not require painting and pass conventional automotive tests with ease; and on the interior we offer a range of finishes that are tough, elegant and recyclable. We are developing a suite of endurance tests to really challenge the longevity of our materials. We compare them to the highest-quality automotive exterior and interior components, to ensure that the material technologies we are employing enhance user experience throughout the life of the vehicle.
We are now in the process of scaling up our developments to full production lines. The experiments that were carried out in the lab are now executed by robots. Small samples have become full body systems built from textiles. We created a vision of the future that is rapidly becoming a reality we are very proud to be a part of.
— — — — —
For more information on Arrival visit our website.
Super Materials for the Next Generation of Electric Vehicles was originally published in Arrival on Medium, where people are continuing the conversation by highlighting and responding to this story.