Embrace the Complexity — An Evolution of Manufacturing
by Doug Morton
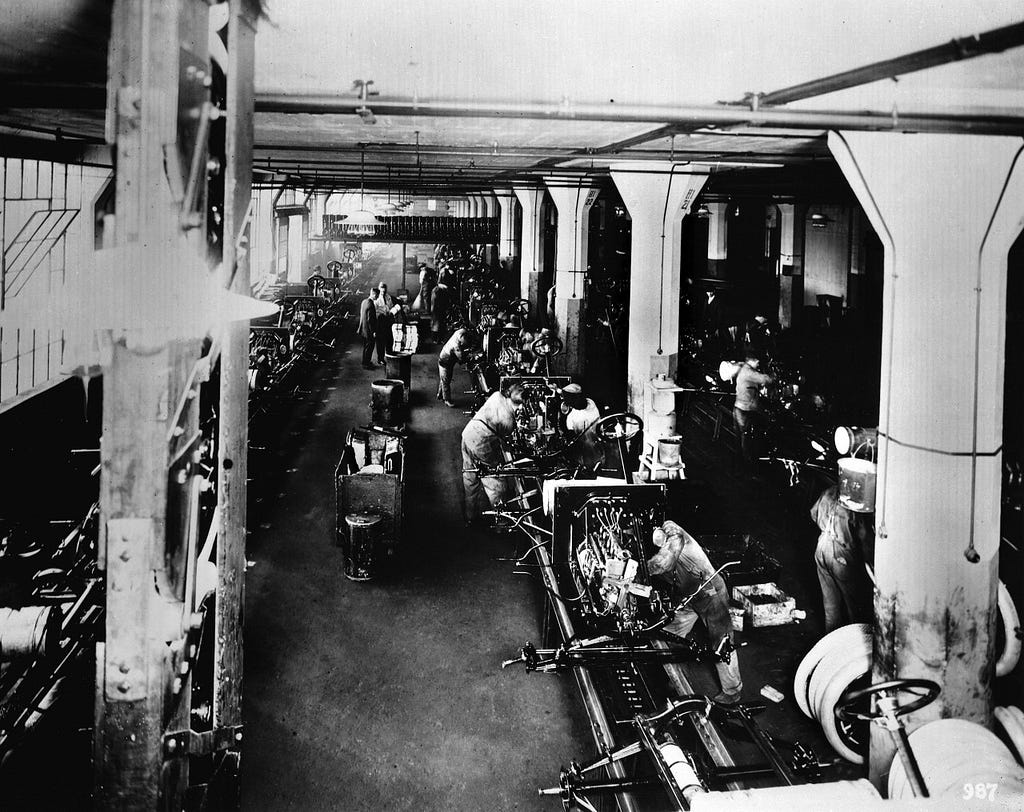
The fixed assembly line has served us well for more than a century, and yet we could unlock a new level of productivity by embracing the unpredictable nature of organic systems. But first, we have to learn to let go.
Humans are creatures of habit: predictability is essential to our productivity. The production line is a masterclass in limiting variability; the process steps are clearly sequenced and the provision of parts carefully controlled — nothing is left to chance.
Manufacturing processes have evolved, with increasing precision, through iterations over time. These advances in reliability and throughput have been achieved with ever closer control. Each stage is clearly defined and sequenced, so that every part of the process is predictable and simple enough to be managed and optimised.
Pre-programmed robots offer superior repeatability for certain tasks, but suffer from their own inflexibility. Optimised for rhythm, neither cope well when they are faced with a situation that appears different to what they expected.
For this reason, manufacturing processes are kept within the constraints of making sense to the people overseeing the design and operation, even though the thing that we really care about in manufacturing is efficient and robust output. If we could liberate ourselves from the constraints of having to make sense to someone, we could then unlock the potential which lies in the spaces between things, the gaps in time, and the natural variations.
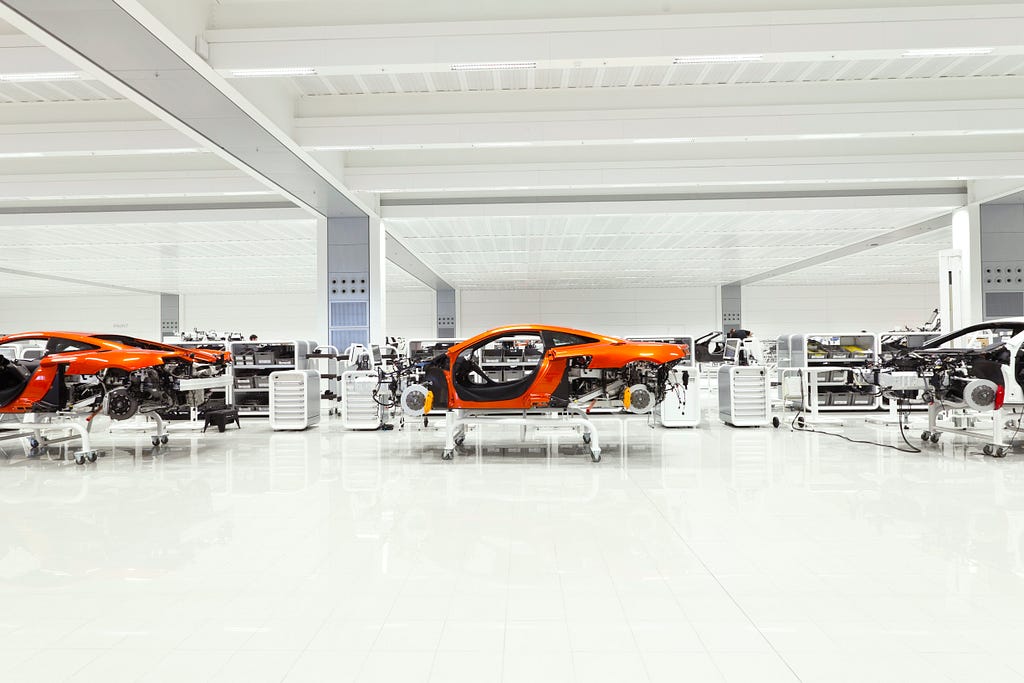
The best place to look for success in complexity is the highly optimised systems that have evolved through the process of natural selection. Ecosystems and biological communities have no responsibility to make sense to someone, and yet make effective use of all available resources in a way which designed structures and systems do not. Natural systems are remarkably efficient, despite being hard for us to comprehend.
Natural systems achieve staggering reliability in the face of a great number of random factors: their survival depends on it. The elements which comprise these systems — such as insects in a colony, neurons in our brain, regulatory genes in our cells — are individually far from reliable, but as a network of autonomous elements, they perform brilliantly.
For example, the replication of DNA is essential to the growth of organisms and is one of the most astonishing processes — not least because of the speed and accuracy. Around a dozen proteins work together as chemical machines handling a staggering 700 base pairs every second, making just one mistake for every ten billion nucleotides copied: this is equivalent to an unimaginable 7.5 sigma in lean manufacturing quality management!

When applied to manufacturing, it’s clear that the factories of the future will not be the organised, tidy spaces we see today — with walkways separating neat lines of plant and predictable storage areas for parts or tools. There is no objective benefit to fixing the process layout, assembly sequence, component orientation, or even the location of tools; these current constraints are fundamentally driven by our inability to cope with variability.
Instead, the production facilities of the future, with every square metre optimised for output, will begin to resemble the micro-mechanical activity of a cell or the frenzy of a forest floor.
Because, put simply, the next step for manufacturing is to build systems where the complexity of design and operation exceeds our capacity to understand it.
Curating desired outcomes and entrusting the finer details of design to a machine, whilst currently unfamiliar in hardware design and manufacturing, is already the preferred approach in the digital world. The best way to solve complex software challenges is to give computers the ability to learn without being explicitly programmed. Rather than design each element manually, we define the rules and desired outcome, training the machine to make use of data to optimise everything in between.
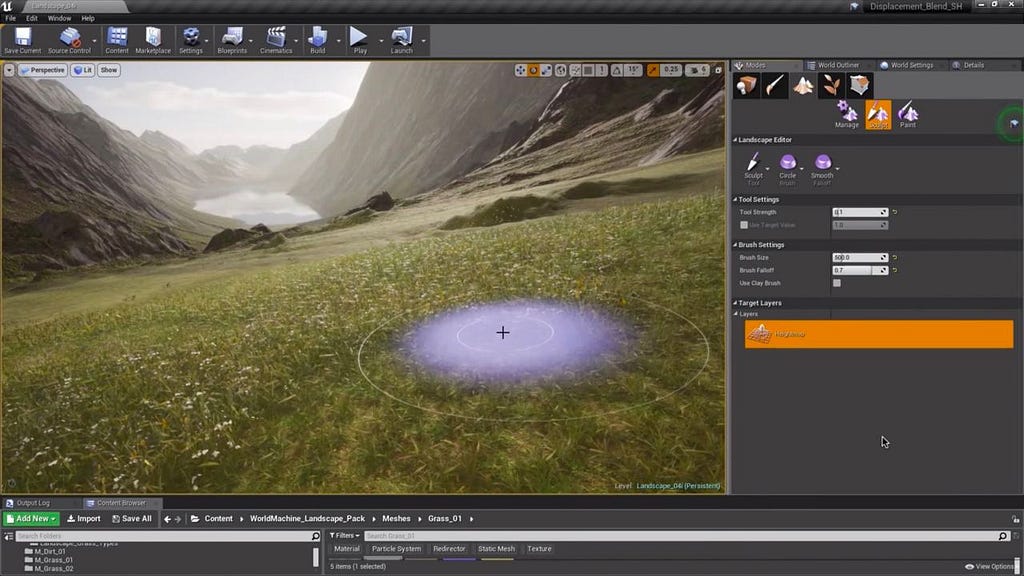
The commercial benefits of a flexible manufacturing approach extend beyond improving efficiency and resilience. Dynamic, self-organising systems adapt to variability in supply and allow for the manufacture of different products in the same facility, customised to meet individual needs. Facilities in different locations with the ability to restructure themselves will be able to maximise the efficient use of available resources, optimising for sustainability. Products can be brought to market more quickly to meet changes in demand, as well as changes in the availability and price of materials, the environment and the macroeconomic landscape.
An optimal system has no responsibility to make sense to us, nevertheless we fight to understand and control every aspect of the design, limiting the complexity and speed of systems to comply with the bandwidth of human cognition. If we as designers can learn to let go — to define the outcome and not the operation — then the factories of the future might begin to approach the efficiency and resilience of the natural systems we want them to resemble.
Doug Morton is Arrival’s Head of Strategic Technology. For more information on Arrival visit our website.
Embrace the Complexity — An Evolution of Manufacturing was originally published in Arrival on Medium, where people are continuing the conversation by highlighting and responding to this story.