At Smart Factory Expo 2022, Rashitha Jayasekara, Chief of Digital Manufacturing, Rolls-Royce, explained how the company is using data within its manufacturing processes and why the government is assisting with funding.
Within manufacturing, there is a huge opportunity to leverage data to tackle inefficiencies, including the burgeoning skills gap, identify cost savings and drive digital transformation – especially in today’s economic climate.
Rashitha discussed these opportunities while offering a blueprint and tangible next steps to build operating models that show a rapid return on investment around recruitment and training, as well as how to access the funding needed to achieve this. He sat down with The Manufacturer at Smart Factory Expo to explain more.
To view a video of the interview with Rashitha Jayasekara click here.
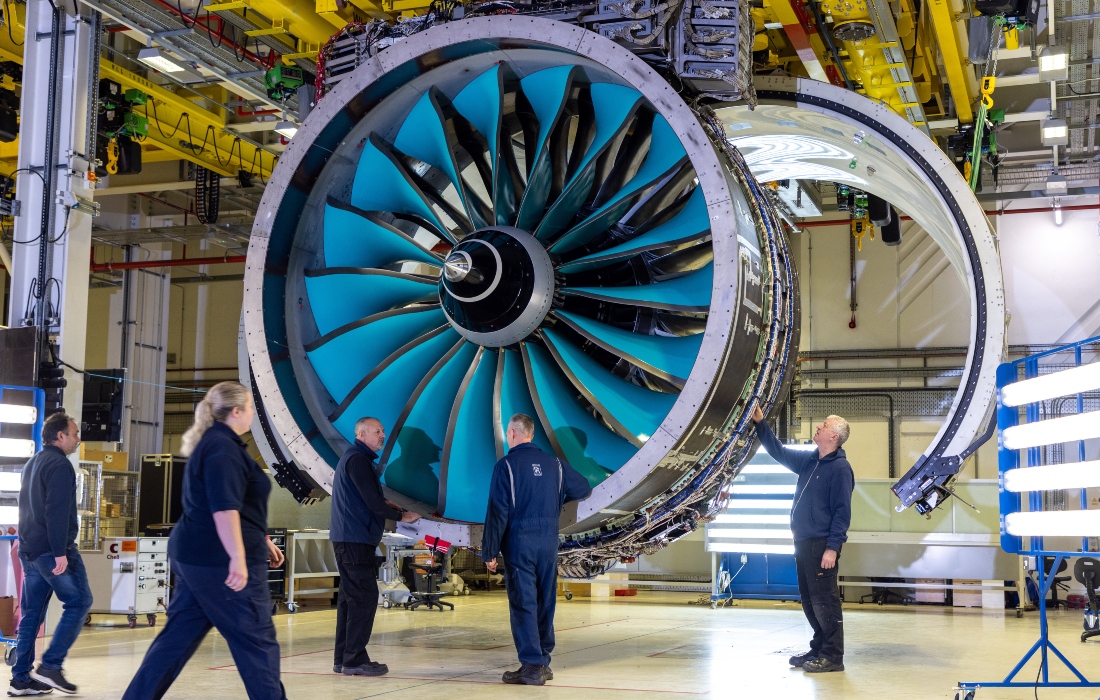
Can you give some background on your talk at Smart Factory Expo?
It’s all about skills. These days we talk a lot about how the digital skills gap is affecting our ability to scale initiatives and bring the next level of transformation within manufacturing. Currently, we are proactively making interventions to the organisation and skill planning, to make sure we are reskilling people who are already working for Rolls-Royce and that they’re ready to take that next step.
We’re using government funding and utilising the Apprenticeship Levy to drive that programme within England. So, we have partnered with a tech start-up called Multiverse, which provides digital apprenticeships, and they have a very unique method of delivering training and identifying skills gap. That’s really important for us.
It’s a data led approach which enables us to really tune into the organisation and find out where we need to deploy skills to have the maximum impact. We’ve combined the data from a skills survey from Multiverse with our traditional skills planning information, and that gives us a more enhanced view of how to get the most out of our investment in technology.
At Rolls-Royce, while we have varying degrees of maturity in our smart factory and digital manufacturing capabilities in general, we have been working on it for the last 20 years, so we have some great capabilities that will enable us to go to the next level. However, the skills gap is our biggest barrier.
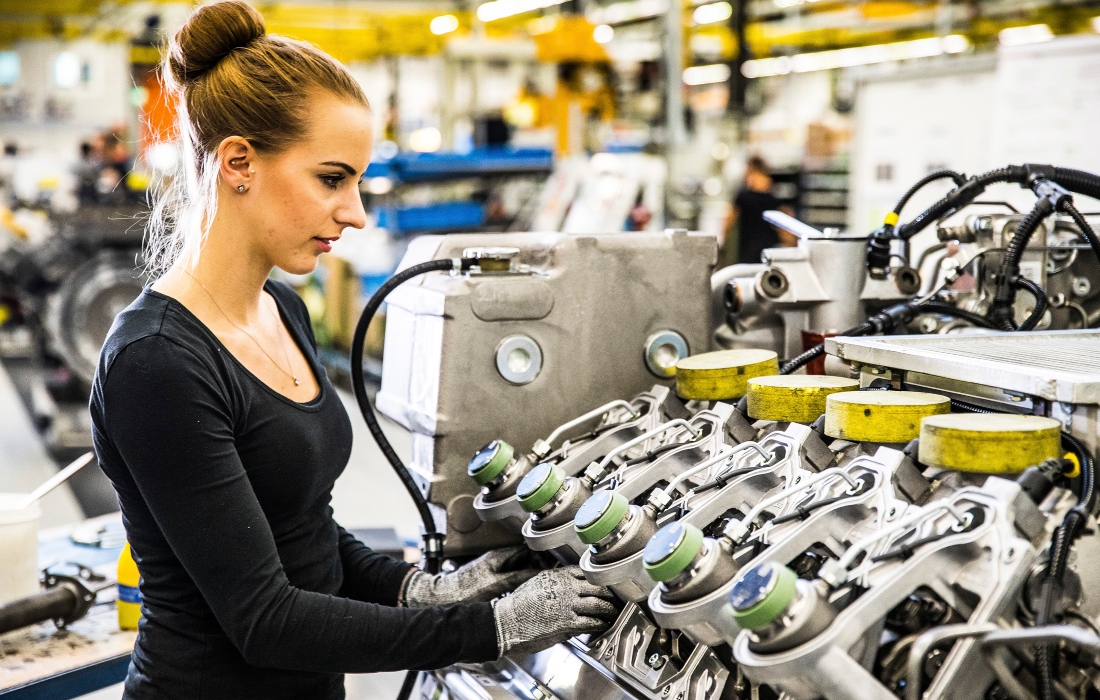
What we’re doing, with the help of government funding, is making interventions to the organisation proactively and ensuring that people who are already working in our space are being equipped with the digital skills required.
For me, particularly for disciplines like data science, we need to combine mathematical skills and domain knowledge, with computer science skills. A lot of our engineers have mathematical skills already, because they’re engineers and are experts in their field. So, they have the domain knowledge, but what they’re missing is the ability to code and to operate using modern digital capabilities. Through the work with Multiverse and government funding, we are enabling that component.
Why reskill rather than recruit?
In truth we need to do both, and we have done so. But right now, there just aren’t enough digitally skilled individuals that we can recruit into manufacturing. That has to change because we need the thought diversity of an individual whose background is not in manufacturing to come into the sector and look at it through a different lens.
At the same time, when we bring in somebody like that, they typically don’t have the domain knowledge or the mathematical skills awareness, which is important to solve big, complex problems. We have discovered that we need to bring in the disruptors to show us different perspectives so we’re not blind to certain aspects. But to truly scale, we can’t just keep buying resources in. Rather, we will have to reskill our current population. I would say 90% of our future digital capability will come from people we already have.
What does the current recruitment landscape look like?
One of the beauties of digital skills is that they are generally industry agnostic and the skills are transferrable; that means they are in high demand. Somebody with the digital skills to an advanced level in manufacturing, can transition into a different sector quite easily. And they can learn about a sector quickly and be really successful. Therefore, manufacturing has a real challenge in attracting those individuals.
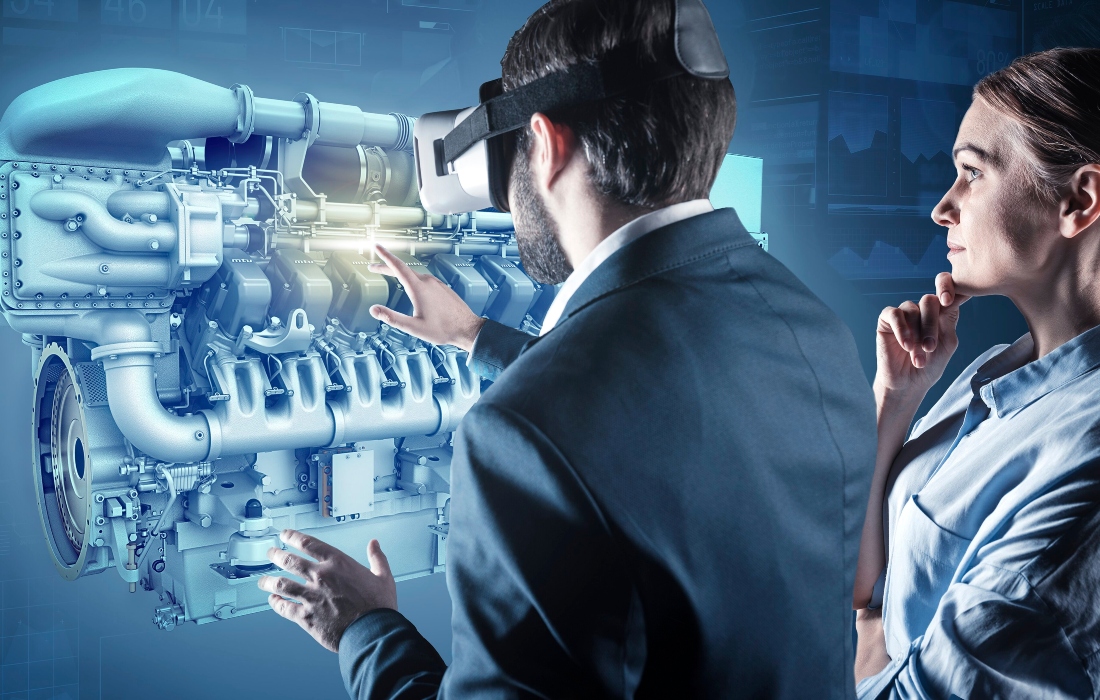
And it’s really hard; if you look at our job board, we have multiple digital manufacturing vacancies, stretching all the way up to chief of digital manufacturing. However, we are finding it really difficult to fill them. That’s a shame because digital allows us to create different products and services that we weren’t able to do before, enabling us to bring additional revenue streams online.
It also allows us to be more productive and efficient, and in general, to do things better. Thirdly, and most importantly, it allows us to shift significantly towards areas like sustainability. With digital technologies we can really understand what our sustainable action plan needs to look like and how to implement it.
What financial help is available?
We’re lucky because we already have very strong links into government initiatives like apprenticeships. So, we already have that infrastructure administration available to us through the Rolls-Royce Apprenticeship Academy.
For people who are not aware of that, and who want to get involved, I would suggest engaging with government (if a relationship already exists), or simply reach out to the apprenticeship organisations to understand how you can access funding. It’s definitely worth investigating whether you are eligible to draw funding, because that allows you to scale your digital transformation programme from a skills perspective, which is effectively cost neutral to you.
You still need to let the people invest the time, and this is where we have been really fortunate in this space; we can invest time for individuals to go and develop themselves. After that we can immediately get them to apply those skills and create more efficiency and benefits to the organisation.
For more stories on Industrial Data & AI click here.