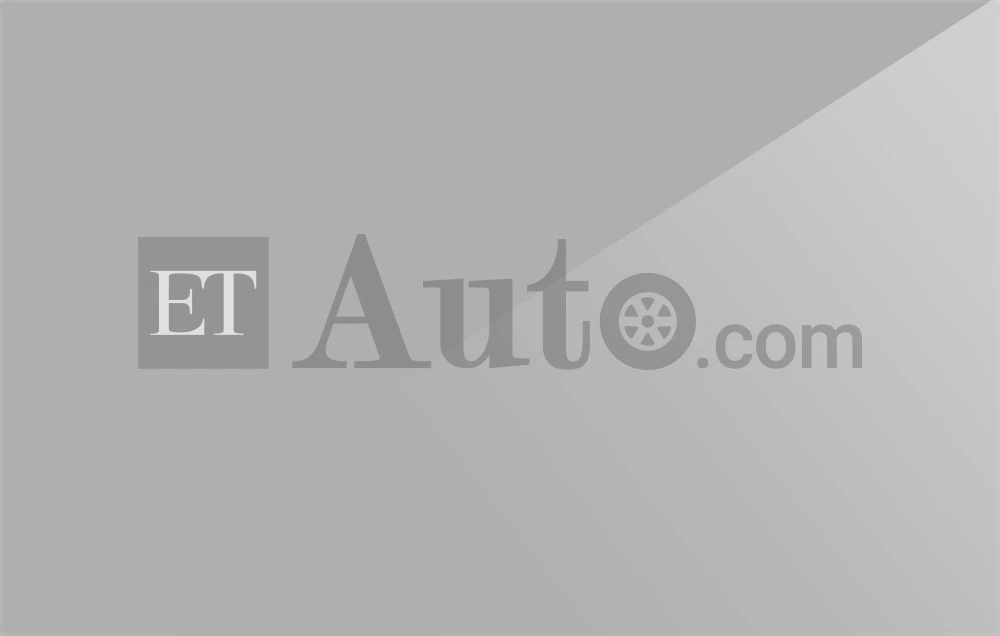
New Delhi: When Bajaj Auto’s Chakan plant near Pune was recently given the award for word class TPM achievement, it was a proud moment for the entire team. After all, this marked the highest level of achievement in total productive maintenance as acknowledged by the Japanese Institute of Plant Maintenance (JIPM).
Pradeep Shrivastava, Executive Director of Bajaj Auto, is as delighted but reiterates that one needs to look at the larger picture too. “We were not chasing this award. What is more important is what TPM does to people in terms of mindset improvement, eliminating losses proactively etc. As a result of doing better, you just apply for the award to keep people motivated,” he says.
The company has been practising TPM at Chakan since 2004 and during this time has bagged all levels of the award. The 2023 Global Leaders initiative, again awarded by JIPM, is “like a jury award” where the people concerned look at other parameters like “your progress, spread and depth of TPM”.
In simple terms, TPM strives for greater equipment efficiencies with complete support coming from the organisation and across hierarchies. In reality, it is way more complex and profound as a science where there is really no final destination with the journey still continuing.
The Chakan facility is often referred to as Bajaj Auto’s manufacturing powerhouse which catapulted it to new heights in the global arena. When the company first entered into a strategic alliance with KTM of Austria way back in 2007, Chakan was chosen as the base to develop smaller capacity KTM-branded motorcycles (125cc-400cc) for overseas markets.
Pride of place
It was also home to the Pulsar, the sports motorcycle brand which is still going strong and was a significant part of the company’s turnaround story. Today, Bajaj has commissioned its second plant at Chakan and has rebooted its traditional scooter facility in Akurdi (again near Pune) which will now house the electric Chetak.
Its other plant in Maharashtra is located at Waluj, Aurangabad, which rolls out its three-wheelers and other bike brands. The fifth plant at Pantnagar in Uttarakhand was commissioned in 2007 and makes a range of motorcycles.
As Shrivastava says, Bajaj actually started its TPM journey at Akurdi which became defunct when production of geared scooters came to a halt. It has now got a new makeover as the electric hub. The TPM exercise then extended to Waluj and Pantnangar though Chakan has been the fastest to reach the top in the excellence category.
The commercial vehicle and motorcycle divisions at Waluj have raised the audit for the advanced special award which is one level lower than the world class.“Both will hopefully have their final audits done in December and next year start practising for the world class award. Pantnagar is two levels below world class and will apply in December 2024, audited in 2025 and be in line for the special award in 2026,” says Shrivastava.
By that time, all the older plants will hopefully be at the “special or above” levels and, after three years, go for world class. Chakan 2 has just started last year and so has Chetak Technology at Akurdi which mean they still have many years ahead before they reach the top layer. Chakan 2 will, incidentally, cater to KTM and Triumph, the British motorcycle brand, which has tied up with Bajaj to develop midsize bikes for the world.
Various parameters
As for the TPM audit, the people concerned look at morale, productivity, safety, quality etc from the outside but, internally, also check out enthusiasm levels of employees and the extent to which they participate “which is more important”. Shrivastava recalls the days when the exercise kicked off in in 2004 and it was a smaller team with everyone completely involved.
“The most important part here is the reviews you do and targets you set. The team sits together, brainstorms and checks out ideas in order to achieve the goals set. Once you get into the cycle, you get deeper into it because you start believing in it. Every new person at Bajaj became part of TPM once they realised it helped them deliver results,” he says.
TPM became so ingrained in terms of delivering on potential that employees began practising it beyond their workplace to homes and gardens. “It involves everyone and is an investment-light proposition. Instead of installing a new machine, you can optimise productivity instead,” explains Shrivastava.
Within the Bajaj Auto ecosystem, there are two distinct buckets: a) deepening and widening; and b) evolving. In the former, the focus is on eliminating losses while the latter has more specific challenges in addressing global models and doing a SWOT (strengths, weaknesses, opportunities and threats) analysis. “To improve weaknesses, TPM has all the tools. It is constantly important to keep focusing while we enter other markets,” he adds.
In the case of Bajaj Auto, this is especially daunting since it exports over two million units annually. There are different models for different countries and the numbers have only increased over the years. It is here that TPM has been a huge help in terms of generating greater efficiencies, reducing losses and becoming more flexible with machinery, systems etc.
Pushing the envelope
“You need to be agile too and once all this in place, the team knows what to do,” says Shrivastava. They will come up with thousands of improvements and the same number of people, machines and lines can comfortably handle the needs of larger export numbers. “If I need more output from this plant at Chakan, the various teams involved will be more than ready to rise to the occasion with their supplier and plant teams at a nominal cost. This is how we have leveraged TPM for improvement,” he explains.
It goes beyond the manufacturer to encompass an aligned supply chain that has the same levels of competencies, agility and efficiency and can deliver any part to any brand be it KTM, Triumph or Bajaj. “We have our own manufacturing processes and systems so that everything is perfect and in sync in terms of generating world class products,” says Shrivastava.
It is also well known within the auto industry that Bajaj Auto’s EBITDA margins are among the highest. Part of this can once again be attributed to its TPM initiatives and cost control. There are many costs in factories, especially in the area of materials, and each improvement causes huge savings which consequently leads to higher profits.
The company has also initiated TPM at dealerships and workshops with the focus on customer satisfaction, profitability and reduced costs. By the end of the day, employees should be skilled, knowledgeable and ensure that there is no loss incurred anywhere by way of immediate corrective action. Two, the supply chain needs to be aligned so that vendors can help each other. Three, building dynamic capabilities is also key and, as and when demand comes, it is important to leverage the talent in the ecosystem.
Shrivastava then narrates an incident going back to 2017 when the Maharashtra government opened up permits for 3-wheelers and demand for CNG vehicles went through the roof. “We had a capacity to produce 50,000 3-wheelers and, in three months while including our vendors’ capacities, enhanced it to 70,000. In the process, we increased our market share by 1% and this is the kind of dynamic capability I am talking about,” he says.