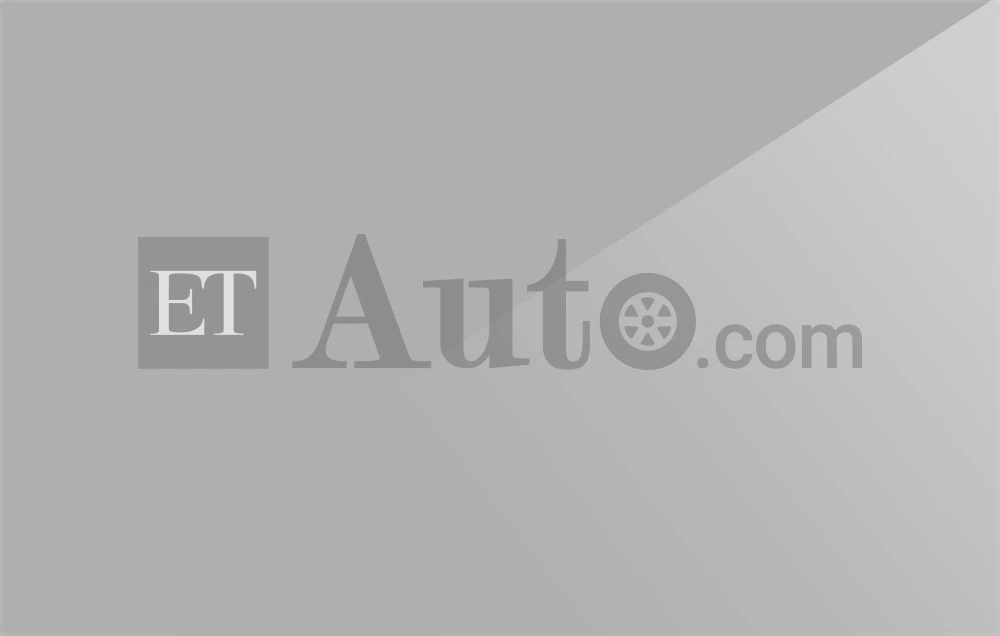
New Delhi: BASF, the largest chemical producer in the world and headquartered in Germany, is betting big on the Indian automotive market for its next phase of growth. The company recently inaugurated its polyurethane technical development centre in Navi Mumbai to support applications in transportation, construction, footwear, appliances and furniture.
“We have a very strong track record of the polyurethane business in India. There is now a need for further innovations and with this centre, we will be able to support our customers with innovations and further material development in the polyurethane business,” Andy Postlethwaite, Senior Vice President, Performance Materials, BASF South East Asia, told ETAuto.
Specifically, for the auto industry, the company’s product range includes engineering plastics, polyurethane and specialty foams, coatings, pigments, catalysts, axle and transmission lubricants, fuel additives, coolants and brake fluids, as well as battery materials.
Additionally, for buses, BASF offers solutions right from brand-impact coatings, chassis and battery technologies to lightweight flooring, lubricants, sealants and adhesives. In India, the company has facilities in Dahej, Mangaluru, Thane, Hyderabad and Chennai.
Electric mobility
“From BASF’s point of view, the footwear market is unique to India but so is the automotive industry where the transition is something we need to keep a track on. This is because we have considerable business going with the internal combustion engine (ICE),” said Postlethwaite.
BASF has been doing a lot of preparation for the change now underway from ICE to other clean fuel options with electric leading the way. The good part about polyurethane is that it can be used in multiple applications. “We have developed many such uses for EVs in China,” he said. By the end of the day, China is the centre of EV development and the biggest market by “a long way” which also meets the needs of batteries and technologies worldwide.
S Krithikumar, Business Director, Performance Materials, BASF India, said the move to electric mobility marked a “learning curve” for vehicle manufacturers and suppliers. “This new centre will help by way of quick experiments and a lot of learnings on ICE can be adapted to make it faster,” he added.
In recent times, electric is not being seen as the sole answer for cleaner vehicular emissions with hybrids also perceived as a viable alternative. According to Postlethwaite, Japanese OEMs have a different strategy to clean energy from the well-to-wheel but “if you view from tank-to-wheel, for example, you have a different view”.
Well-to-wheel evaluates efficiency and emissions of an energy source by considering its entire lifecycle. Tank-to-wheel refers to the emissions associated with burning the fuel to power a vehicle.
Supporting all technologies
“Our job is to support the technology irrespective of the view concerned. We need to have solutions for everything including ICE, developed solutions for BEVs and for hybrids, some of which are ICE and EV where you can combine. We need to be adaptable on the move depending on our customer needs,” he said.
One of the main technologies for the electric vehicle is a cylindrical cell which is “massive”. It was in this context that BASF struck upon a solution using polyurethane potting which was was successful in China.
“There was a similar requirement in India where it was smaller and we adapted the material to suit that application. It is a very nice solution for a two-wheeler company in India. We try to multiply solutions where developments in one region can be attempted elsewhere,” said Postlethwaite.
BASF has multiple divisions catering to automotive across its entities worldwide where they share information and “door-opening opportunities”. He said he was even more optimistic about the Indian auto industry seeing the pace of growth, improvement in quality and the role of the country as a global hub.
“We know there is a strong drive towards Make in India and we must invest constantly to expand our products and services including capacity, capabilities and chemicals,” said Postlethwaite. With changing times, a chemicals company like BASF would need more mechanical and electrical engineers accompanied by different kinds of expertise with peripheral knowledge of materials.
“Artificial intelligence is another topic that could benefit R&D and we see a lot of opportunities that could complement human capital,” signed off Postlethwaite.