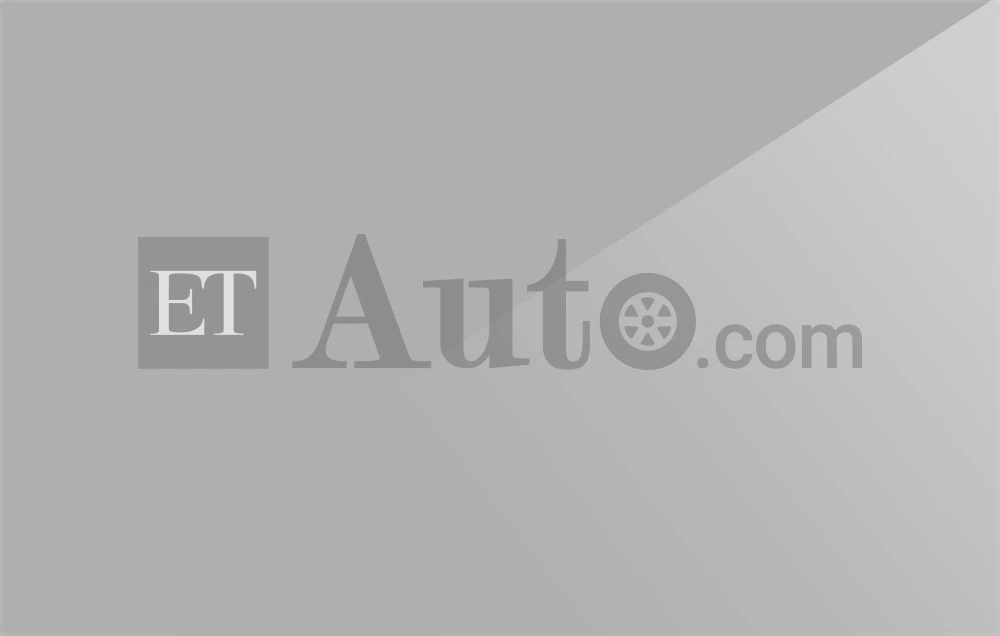
New Delhi: Pawan Goenka smiles when the topic switches to the ideal clean fuel for India’s automobile industry which he terms “a multibillion dollar question and the big elephant in the room”.
The former Managing Director of Mahindra & Mahindra, also fondly referred to as the ‘Father of the Scorpio’, is now Chairman of IN-SPACe, Department of Space, Government of India. Yet, it is amply clear that he has not lost touch with the auto industry with which he was associated with for many decades, both in India and the US.
“My views have not changed in the last 10 years on what is right for India. This whole talk about hybrids being the intermediate step to electric vehicles makes no sense to me,” says Goenka. As he puts it, there is “nothing that says you should go” from ICE (internal combustion engine) to hybrid ICE and thereon to electric which is tantamount to transiting from Bharat Stage 3 to 4, 5 and 6 emission norms.
“When the technology was ripe for BS 6, there was no reason to make a stopover at BS 5. The same thing holds true now: when hybrids came, electrics were nonexistent but now EVs are here,” he says.
Electric the best bet
According to Goenka, electric serves two purposes: achieving zero pollution in cities and reducing oil imports. Hybrids reduce imports by 15% and pollution by 10% but not zero. “Why would you want to go from 100 to 85 when you can go from 100 to zero?” he wonders.
Having said that, the only argument in favour of hybrids is that electrics are not taking off at the pace they ought to have. There are not enough models in the markets or enough charging infrastructure and the thinking therefore is “let us do hybrids meanwhile”.
However, by doing so, “we are basically creating a distraction” and the focus should instead be to go all out with charging infrastructure — whether it is led by the Centre or private sector. Somebody should ideally put their best foot forward and assure stakeholders that within the next two years, India will have no worries on this front.
Whoever takes up this responsibility should ensure that India does not suffer for want of charging infrastructure. “Whatever needs to be done must be done to make this a reality and it is definitely doable,” reiterates Goenka.
GST realities
Beyond this is the issue of cost when it comes to EVs. Despite the concessional 5% GST levy, their selling price is still higher than ICE models and hybrids. As he says, retaining this 5% is not sustainable in the long run given that GST collections from auto form a big chunk of the Centre’s revenue which is hard to forego.
The good news, however, is that lithium prices have crashed and experts say they will not get back to the levels they were. Lithium is also “totally recyclable” and once the recycling setup is in place, there will be enough in place while transiting from one battery to the next.
Given this backdrop, lithium is not a concern and, hopefully, there should be no adverse geopolitical situation that comes in the way of getting these metals that go into the battery.
“We should be able to bring costs down and the reasons why they still haven’t fallen is because they are largely imported. We have to be self reliant on motors and magnets and we can since India has the third largest deposit of rare earth metal that goes into making magnets,” elaborates Goenka.
Focus on localisation
Yet, not a single rare earth magnet is made in India because all of that deposit is exported and value-added outside. A motor has to be 100% local where the magnets are made in India and “there is no reason why we cannot do so”. This is the second most expensive part of an EV.
Battery modules and assembly are already being done in India and nobody “should be allowed” to assemble batteries outside and bring them here. The third aspect of the costing structure is the cell and this will hopefully become real in the next three years as companies set up their own cell plants.
Power electronics is another significant cost in EVs and Goenka believes that India has enough ability to make them locally but the problem is scale “because we don’t have enough today”. If India is 50% EVs a decade from now translating into four million units annually, there will be enough scale to develop power electronics. Effectively, if the motor, battery and power electronics are done in India, costs will go down. “Availability and capability are not issues but scale,” stresses Goenka.
Going back in time
While conceding the point that China is comfortably ahead at this point in time, he reminds you that two decades ago, when the Indian auto industry had had just started making components locally, “the same argument could have been made then”. Quality was also an issue..there was no technology, no capability “and yet we got over all that”.
It took efforts from industry leaders to say this was in the country’s long term interests else “we would have remained an auto industry with dependence from outside”. The same sort of thing has to happen today where the industry and government must work together — away from individual short term interests — and more for how India can become the capital of EVs globally.
“When India got into vehicles, we were way behind the world but in EVs, we are just a little behind and this is our chance to make a mark,” says Goenka. It is also likely that at some point in time, this will become mandatory by the Centre which has been supportive so far with 5% GST, PLI, FAME 2 etc. “What more do you want?” he wonders.
According to him, not many people are really concerned about the risks of pricey oil imports and pollution. “We should make electric a reality and not vacillate..a lot has happened but the outcome is little. We have to see some serious increase in EV volumes over the next 3-4 years..not 10-15%,” says Goenka. At present, electric penetration is just 2% in cars while two and three-wheelers are doing a lot better.
Living without sops
Going forward, the challenge is to keep in mind that the sops for electric will not be around permanently and “you need to make it cost-justified for the user without the benefit of subsidy”. Perhaps, the near future will see EV manufacturers pay 18% GST, up from the present 5%, without any incentives. The only way out then is to bring costs down and bring about a 13% improvement (in the cost structure) to make EVs sustainable on their own.
Beyond electric, Goenka believes that the Indian automobile industry has come a long way in terms of volumes, technology, supplier base, quality, features, managing price points etc. “We have done extremely well and must be proud of what we have achieved. However, we are not doing enough in exports from India,” he rues.
Total exports of cars are only 13-14% which are a lot lower than Korea, Germany and Japan. Goenka says this is unacceptable given that India has strengths like low costs, improved quality that is near global standards as well as emission and safety norms that are at par with the world’s best.
“Till 10 years ago, Indian automakers could not have looked at exports because they didn’t have product and quality. Today they do and at a price which is the world’s best,” he adds. The focus, therefore, has to be on brand building where products from homegrown Indian companies should not be seen as being cheap but inexpensive and good.
MNCs must do more
As for other multinational carmakers, they should see India as a place to manufacture and export. After all, reckons Goenka, the country has everything in place like quality, skilled manpower etc and the key is to entice these companies into using it more as a manufacturing base. The Centre, meanwhile, can support these efforts by focusing on building the manufacturing brand of India and working towards FTAs where Indian carmakers are not at a disadvantage.
“Industry should set for itself a clear target on increasing exports of vehicles from 14% to a higher number by a certain deadline. It should be really substantial over a 10-year timeframe,” says Goenka,
Moreover, the name of the game should be collaboration and not competition where the likes of Mahindra and Tata are not competing with each other but with the Chinese. “They should see how they can collaborate while exporting and not do anything which leads to collusion. The focus should be on competitive collaboration,” he explains.
Finally, on the components side, India exports $25 billion worth of parts and imports the same value which means zero net exports. Goenka is puzzled that this is happening in a low cost country with the most independent supplier base among developing markets. “How can we have this structure?” he wonders.
The landed cost to Western Europe, the US, Korea and Japan will be at least 10-15% lower from India than any other market. “Even OEMs manufacturing in India will tell you that it is 10-15% less expensive when made in India. We have a cost advantage despite the fact that there are other things that drive up costs,” he explains.
Space vs Auto
Goenka is enjoying himself in the new domain of space and believes that when it comes to product development of a launch vehicle and car, there are lots of similarities in terms of steps, processes, design, testing and specifications. The cycle time is about the same as also the budget.
“One major difference between space and cars is that a spacecraft cannot go to a workshop and it must be designed to last 20 years,” he says. Even if one part fails up there in the sky, it is impossible to even conceive of the aftermath.
The cost of a component for a spacecraft is also more expensive. “How to make things cost-effective is perhaps what space can learn from auto and how to get impeccable quality and reliability is something auto can learn from space,” signs off Goenka.