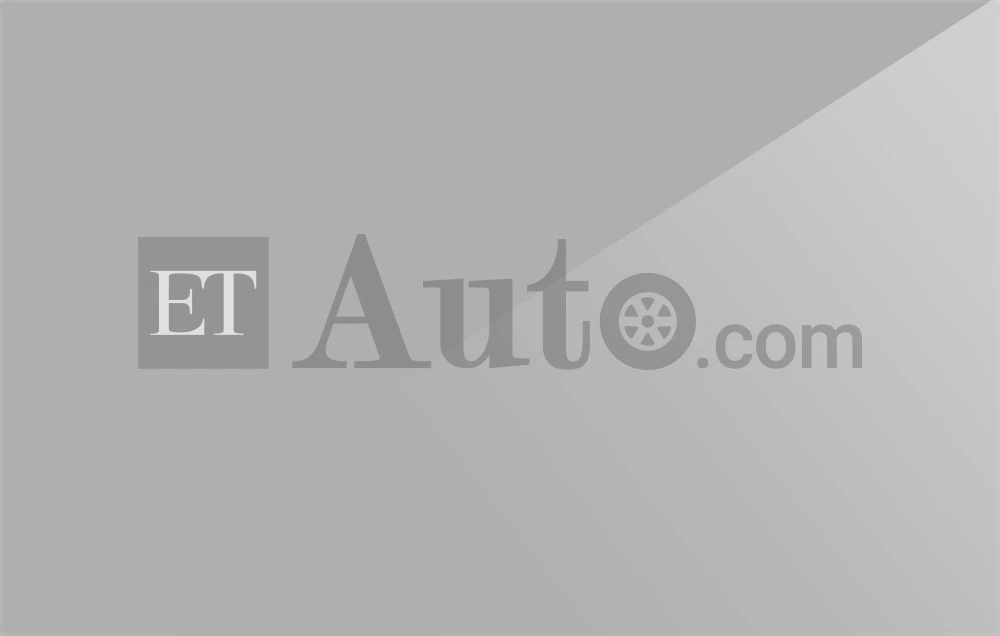
EV manufacturers have been addressing range anxiety with larger battery packs, and building consumer confidence through advanced technology and features, steadily enhancing vehicle capabilities. While this evolution has made EVs more powerful and larger, it has also made them heavier—introducing a “weight penalty” that poses a unique engineering challenge. Manufacturers are now tasked with balancing performance, efficiency, and sustainability—meeting these demands without compromising environmental goals, vehicle agility, safety, or quality.
This calls for a holistic, intelligent approach combining frugal engineering and lightweighting, with a focus on optimising vehicle architecture, topology, material selection, design, manufacturing, and electrical systems.
“Today, EVs can offer over 850km of range, alleviating range anxiety and boosting consumer confidence. However, this has posed a significant challenge for OEMs in optimising vehicle weight, as the batteries are the single largest component contributor to an EV’s mass,” explains Steve Brown, Global Head – Body Engineering CoE, Tata Technologies. He adds that leveraging frugal engineering and lightweighting principles can offer multi-dimensional advantages across design, materials, parts, and manufacturing, impacting not only vehicle performance but also operational costs and environmental footprint.
“Lightweighting significantly reduces the environmental carbon footprint by minimising energy consumption throughout the vehicle’s lifecycle, from material extraction to disposal. We achieved a 15% improvement in energy efficiency for an EV client, resulting in a reduction of approx. 8 tons of CO₂ emissions per vehicle over its lifecycle,” shares Brown, adding that by optimizing designs and integrating parts, the company has helped many OEMs reduce their raw material costs by approx 15-20%.”
Emphasising on the substantial R&D efforts in lightweighting with a focus on sustainability, Deepak NG, MD of Dassault Systèmes India, remarks, “To achieve meaningful weight reductions in EVs, a multi-faceted approach—incorporating alternate material discovery, advanced simulation studies, component reuse across vehicle programs, topology-based lightweighting, and additive materials and manufacturing techniques—needs to be leveraged.”
He adds that optimising battery pack design for strength-to-weight efficiency will further boost EV performance and range. “When these strategies are implemented in tandem, EVs can become not only lighter but also more efficient, sustainable, and cost-effective for the future.”
Giving example of Tesla’s battery case structure that eliminates the need for a separate main floor assembly, resulting in significant weight savings, Brown shares, “Optimising material grade and thickness is crucial in EV design to ensure the right material is used in the right place.” Traditional steel-rich architectures have shifted to mixed-metal combinations, using high-strength steel, aluminium castings, carbon fibre, and magnesium to reduce weight while maintaining safety and durability. “Smart use of these materials has enabled up to a 30% weight reduction, as demonstrated in our past experience with European OEMs. As always selection of materials has to balance cost and the capabilities of the local manufacturing infrastructure.”
VG Ramakrishnan, Managing Partner at Avanteum Advisors LLP, emphasises the inherent limitations of lightweighting in EV body and design, stating, “There is a limit to lightweighting—you cannot continue reducing weight solely to enhance efficiency or extend range. You must also consider centre of gravity, stability, safety, and overall product performance.” He notes that battery weight remains the primary challenge in EVs, suggesting that even a 10-12% reduction in battery mass could significantly boost range. According to experts, battery components make up to 60% of the EV’s weight followed by motor at around 15%. Moreover, a 10% reduction in vehicle weight can boost battery range by approx. 6-7%.
“Additionally, the wiring harness is a critical component that contributes to overall weight. By either using alternative materials or enhancing material conductivity, lightweighting efforts in this area could further improve efficiency,” Ramakrishnan adds. Agreeing on the same, Brown notes that by adopting an electrical architecture that uses less copper in wiring harnesses, consolidates modules, and incorporates more energy-efficient processors and components like lighting, manufacturers can achieve notable gains in weight reduction and efficiency.
Deepak NG emphasises that integrating Mechanical, Electrical, Fluidics, and Software disciplines within the context of system requirements and architecture allows for a holistic view of system design. “This cohesive, multidisciplinary framework ensures alignment and convergence towards product performance and market demands,” he explains. “It enables organisations to efficiently evaluate change requests or develop new products and system variants, all while leveraging a unified, performance-based systems engineering approach that ultimately reduces the cost of system and product development.”
Brown notes that a tech-centred focus in EV design has driven significant improvements in user experience and vehicle safety and can also be utilised to enhance efficiency. “The SDV (Software Defined Vehicle) architecture represents a frugal approach,” he explains, “allowing performance upgrades or new feature integrations without the need to replace physical components, thereby reducing both vehicle weight and downtime.”
To learn more about the electric vehicle ecosystem and meet the key industry leaders, click here.