We go inside the plant where the brand’s new history is written: this is where the electric revolution starts for VW.
This September, at the Frankfurt International Motor Show, the standard version of the Volkswagen ID.3 will be officially presented, the first electric vehicle designed for a mass market, with a starting price below 30,000 euros.
***Editor’s Note: This article comes to us via our sister site InsideEVs Italy. It’s been loosely translated here to preserve its style. Check it out on InsideEVs Italy here.
In regards to the ID.3, we now start to have more and more information, such as the capacity of the batteries, but what’s going on behind the scenes? There’s a multi-billion dollar investment plan for the renewal of production facilities. In the video (in Italian, but you can activate English subtitles via YouTube) we tell you what is the first step of a much larger strategy, namely the restructuring of the Zwickau plant, which we visited right in the middle of the reconversion process that will lead it from the production of the Golf to that of the ID.3.
Zwickau: not just ID3
It is perhaps not the most famous of the Volkswagen plants but the one in Zwickau, in Saxony, is certainly among the most strategic and is destined to reinforce this importance in future years, given that what will be implemented there will then be replicated at the other plants. Up until now, 300,000 units of Golf and Golf Variant were produced annually in Zwickau, on a total of two production lines and 8,000 employees.
In early 2018, however, work began that will lead the plant to a conversion aimed at the production of electric cars. Not only the aforementioned ID.3, but five other models: two other Volkswagens, two Audis and one Seat, all based on the new modular MEB platform.
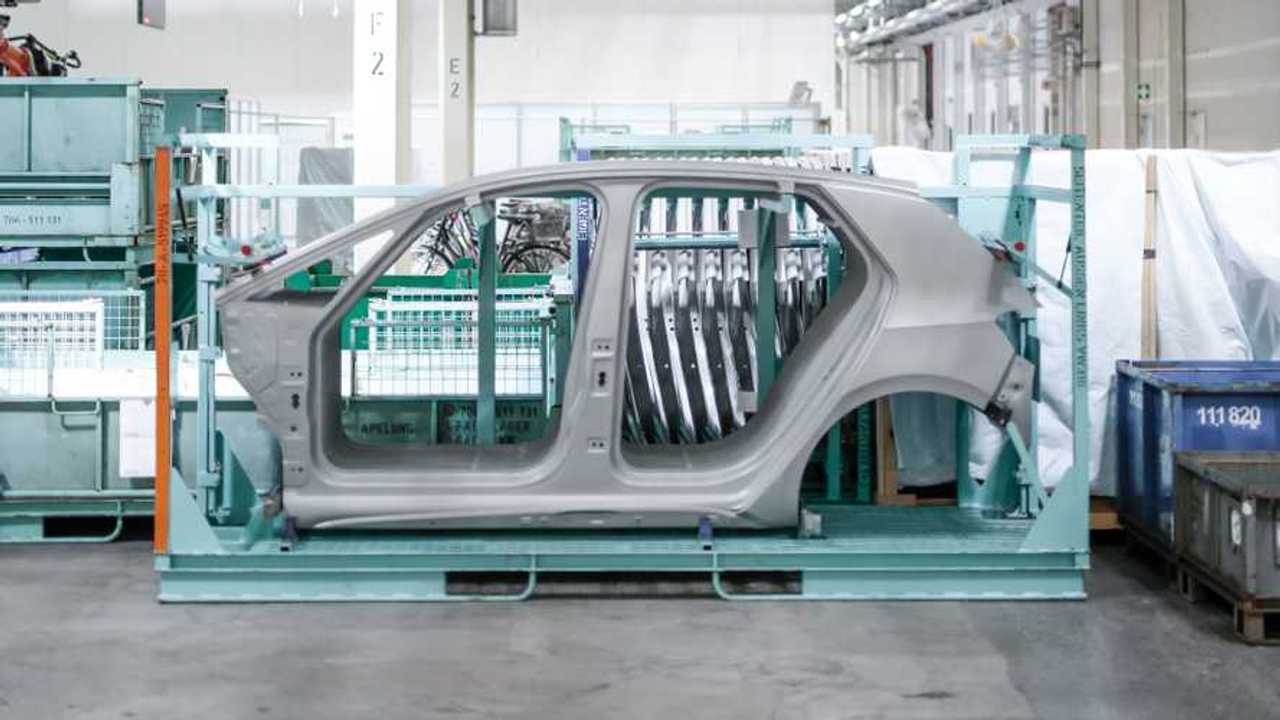
A challenge never faced before
The plant is earmarked for 1.2 billion euros, which will be utilized to hire fifty external companies, who will put to use 9,000 tons of steel and install 1,500 new robots. The employees, on the other hand, will not decrease: the large injection of mechatronics will be offset by the increase in the number of cars produced, which will rise to 330,000.
It would probably have been easier to design an establishment from scratch than to upgrade one that needs to maintain the same current production level. It is therefore critical to alternate between the two production lines at full capacity and on the training of personnel that will be responsible for the new EVs. This will change in 2021 when the plant switches over to mostly electric cars.