FF was established in 2014 with a visionary approach, to transform the way people move and live. From that vision, the remarkable FF 91 was born, a vehicle that truly disrupts the traditional automotive space and in turn demands the highest performance of all its systems.
The foundation beneath the FF 91 is the Variable Platform Architecture (VPA) which was developed at the conception of FF. The goal behind the VPA is to have a robust propulsion architecture that can be modified and fitted into different vehicle applications.
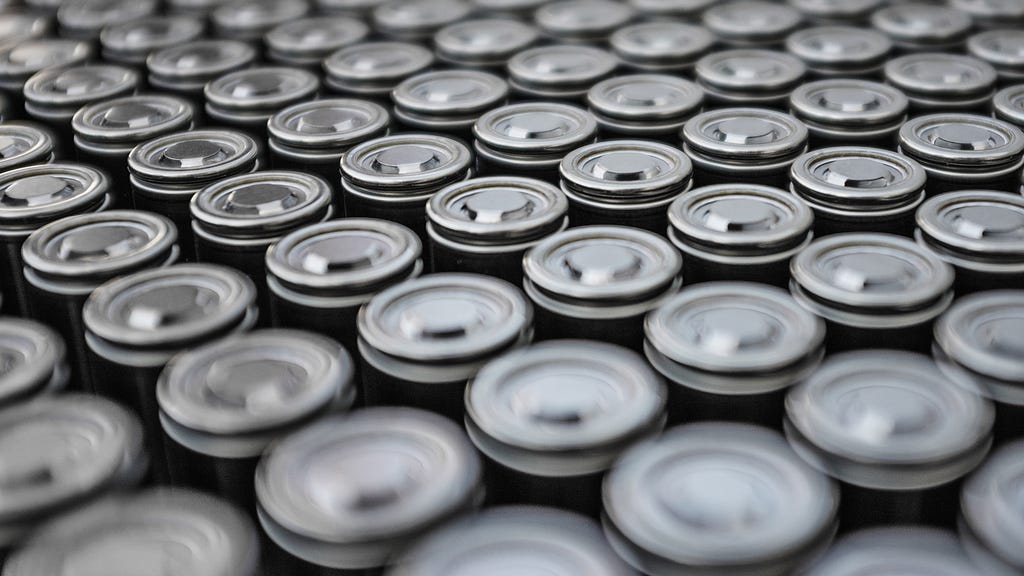
The Battery Pack is a key system of the VPA and in the FF 91 it supports many of the main functions that make it an extraordinary vehicle.
- Over 300 miles of range
- Accelerate from 0 to 60 mph in under 3.0 seconds
- Accelerate a quarter of a mile in less than 10 seconds
- Fast charge at a rate of 500 miles of range per hour
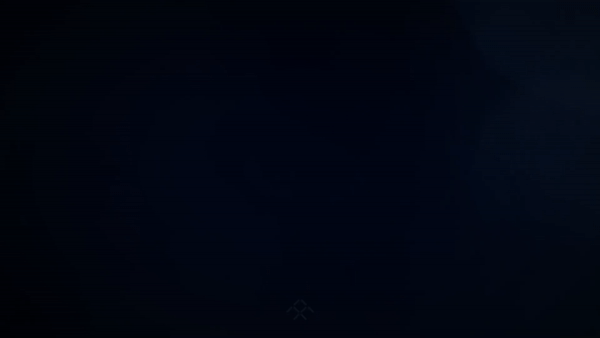
These are some amazing numbers, and they require a sophisticated system to safely and efficiently deliver them. It might not be evident at first, but these requirements are directly tied to the thermal management of the battery pack.
The battery cells perform their best at temperatures near 25°C (77°F), and, as they release or store energy, they tend to get hot, so the cooling scheme becomes a crucial part to ensure top performance during the useful life of the vehicle.

As the VPA was designed, we explored numerous different cooling methods. We wanted to have a system that was scalable and more efficient than any other. After a wide-ranging evaluation, our team came up with a unique solution: a fully submerged system.
In 2015 we pioneered a patented cooling scheme where all major battery components are submerged in coolant.
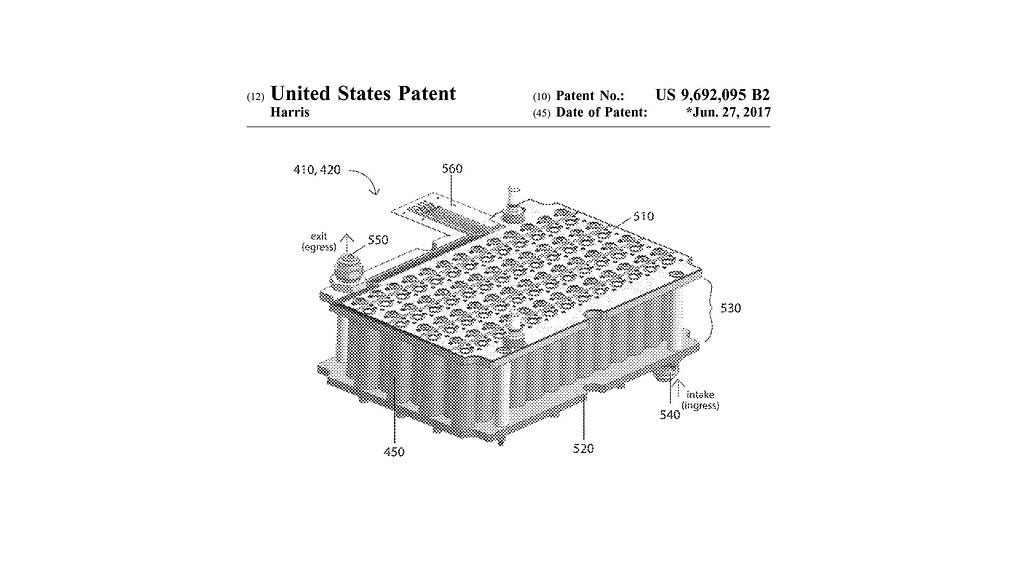
We had to overcome some challenges in our search for a coolant fluid that would meet a set of strong requisites: It had to be compatible with the cells, not be flammable, have low viscosity, and be relatively inexpensive.
The coolant we chose is a non-conductive oil with great thermal properties that allows the pack to have uniform temperature across all its components. With the coolant surrounding every inch of cells, current collectors, and control units, we achieve stable temperatures between modules and strings, enabling the battery pack to better respond to the high demands of our vehicle.
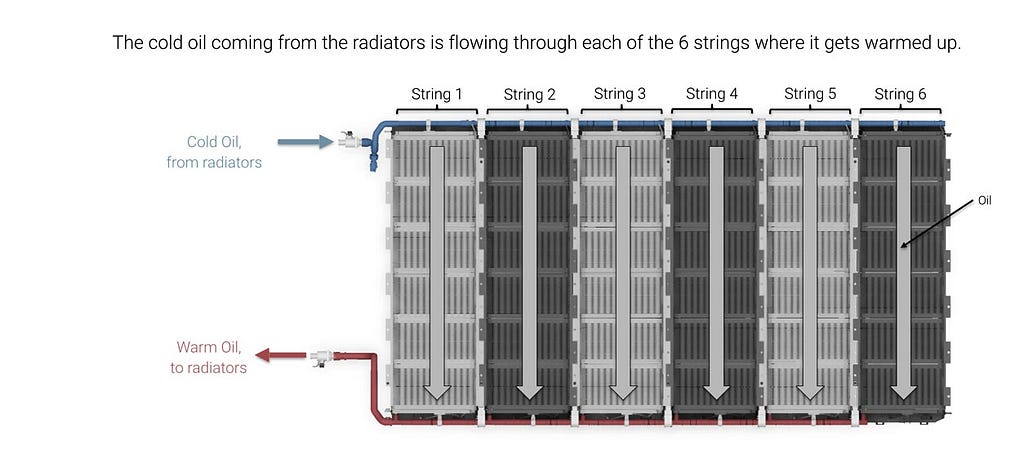
Our cooling system also lets us eliminate the potential risk of corrosion as all electrical components and their connections are submerged in the fluid. And, since we’re working with a liquid, we can reduce the spacing between cells and increase the total energy density of the pack, as the coolant can flow freely even at millimetric distances. Also, it provides a natural dampening effect relative to component vibration.
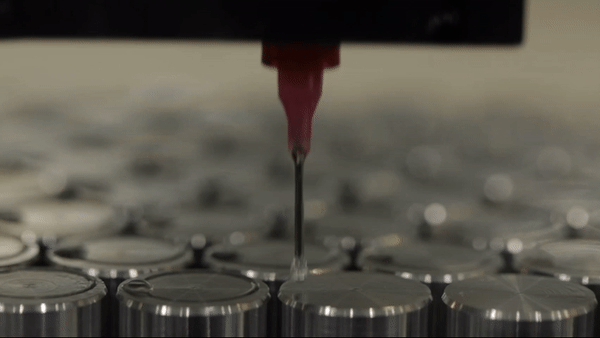
We did extensive testing to make sure that all components in our system — coolant, cells, current collectors, enclosures, etc. — were compatible with each other. We also confirmed through validation that we meet and exceed life cycle requirements with our solution.
Our pack has around 7000 cells, and with our innovative flow pattern design we are able to individually cool each one of them. One of the biggest tests that we put our cooling system through came when we participated in one of the most taxing races in the automotive world: Pikes Peak International Hill Climb.
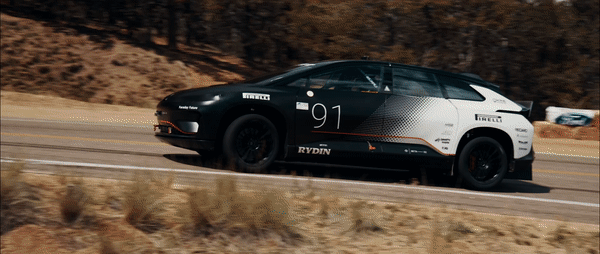
In our run up the formidable Pikes Peak, we established a record (without externally cooling the pack) and demonstrated that our production-intent battery pack can perform in demanding conditions and maintain an optimal environment for the cells. The battery pack that was in the Pikes Peak vehicle is fundamentally the same battery pack that we will be offering to our customers when the vehicle goes on sale.
Our real-life testing didn’t stop with Pikes Peak. We’ve tested our pack in cold weather, drove it through Death Valley, from Los Angeles to Las Vegas without stopping for charging, and accomplished many other test drives on that have given us the confidence to say that our battery pack technology is as robust and reliable as we envisioned it to be when we first started this company.
In summary, FF’s battery technology doesn’t sacrifice range for performance. Outfitted with a 130 kWh battery, FF 91 has an estimated range of over 300 miles. Similarly, the system’s compact design enables more cabin space for greater comfort and safety. FF 91 is also slated to have the fastest charge speed currently available, with an ability to charge at more than 500 miles per hour. The home charger, planned to be included with the vehicle, will achieve a 50 percent to full charge in under 4.5 hours at 240V.
All of these spectacular features are possible thanks to the fully submerged cooling system that we’ve been perfecting for over five years.
Everything about our cutting-edge vehicle and technology was created to make the lives of our users more connected, more engaging, and more effortless.
- Production FF 91 specifications may differ from those discussed here.
About the Author
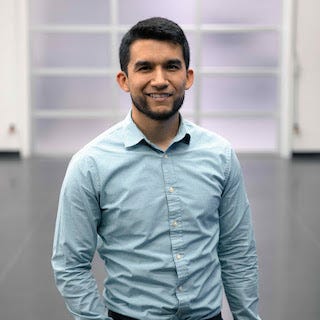
Oscar Trujillo is a Battery Validation Engineer on FF’s Energy Storage and Charging team. He contributes to the design, testing, and final validation of the battery system. Oscar has over a decade of experience in the automotive industry and vehicle technology, leading projects for American and German automakers.