Performance sports car manufacturer Porsche has worked with machine tool producer TRUMPF and automotive parts company MAHLE to 3D print pistons for the engine of its flagship 911 supercar.
Utilizing Laser Metal Fusion (LMF) 3D printing, the carmaker’s engineers have been able to optimize the structure of the automotive part for when it’s under load. AI-led additive manufacturing has also enabled Porsche to integrate a cooling duct into the component’s ‘crown.’ These features not only reduced the piston’s weight by ten percent compared to those forged by the company in series production, but they added 30 BHP to the engine’s horsepower.
“Thanks to the new, lighter pistons, we can increase the engine speed, lower the temperature load on the pistons and optimise combustion,” explained Frank Ickinger from the advance drive development department at Porsche. “This makes it possible to get up to 30 PS more power from the 700 PS biturbo engine, while at the same time improving efficiency.”
Additive manufacturing Porsche’s pistons
Utilizing 3D printing instead of conventional production methods to create the pistons, allowed Porsche to focus its use of material in areas where the component was subjected to the highest external forces. This technique made the pistons considerably lighter than those in its current supercars, and produced an extra 30 horsepower from its 3.8-liter twin-turbo engine, revving it up to 730 BHP.
“3D printing allows us to construct items bionically, and produce extremely lightweight, yet high-strength components, which are now helping us to cut out a huge amount of weight in the case of our piston design,” explained Dominik Abele, Project Leader, Corporate Advanced Engineering at MAHLE. “We can now run the engine at a higher RPM, and this generates more power.”
A particular focus was placed on the outer shell of the piston or its ‘skirt,’ and the point at which it meets the part’s ‘conrod’, referred to as its ‘pinball.’ Incorporating a cooling gallery into the component, reducing the temperatures of these areas, and increasing the overall efficiency of the engine too. Moreover, employing AI to optimize the piston’s shape and underlying topology, minimized the need for supporting material. As a result, only the hole for the part’s ‘wrist pin’ needed to be removed later in the process.
Porsche produced six prototype pistons using a high purity M174+ aluminum alloy powder made in-house by MAHLE, and 3D printed them using a TRUMPF 5000 system. In a process taking a total of 12 hours to complete, the part’s 1200 layers were constructed using a laser melting 3D printing technique, which shaped the powder into the final product. The printed pistons then underwent the same preparatory steps as their conventional counterparts: machining, measuring, and testing.
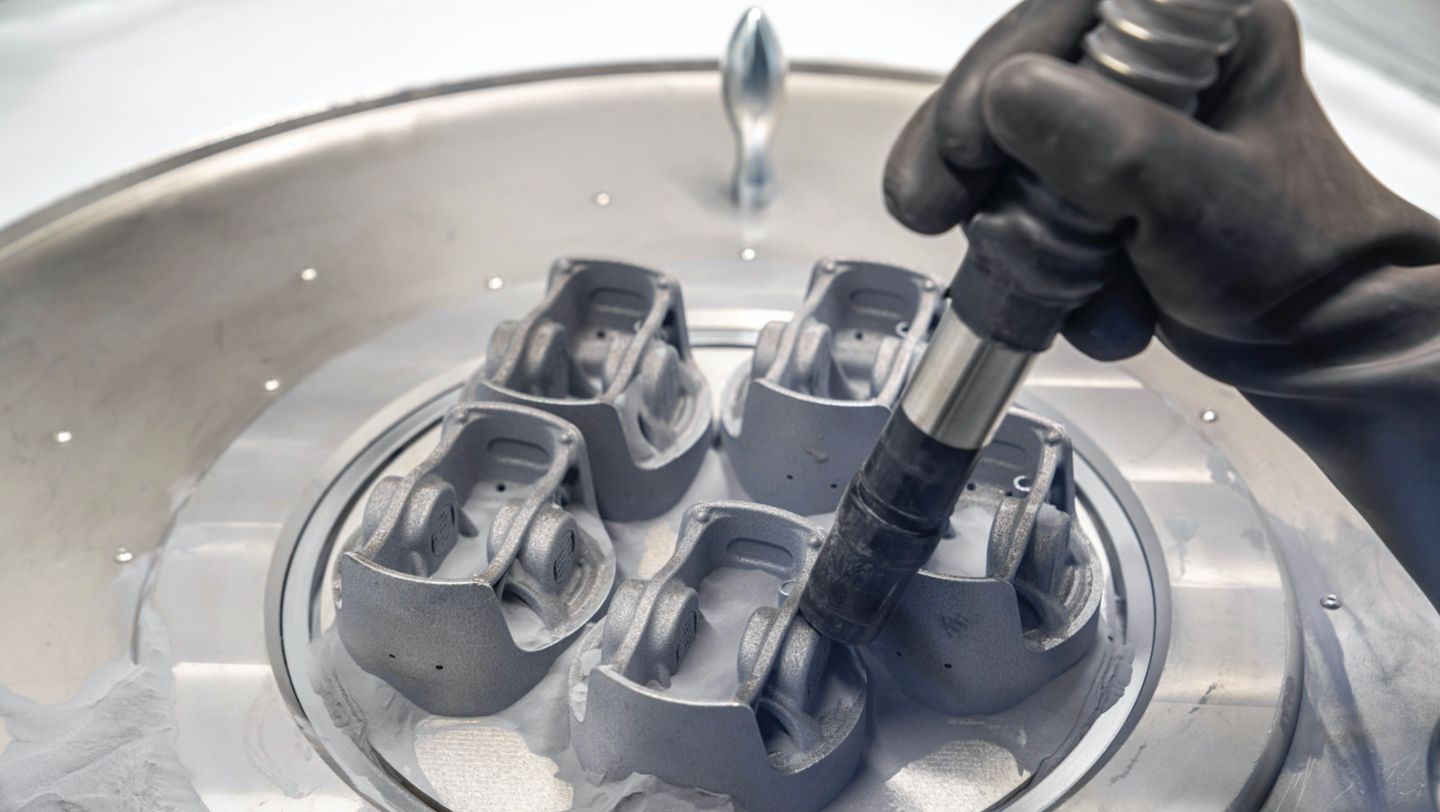
Validating the newly-developed additive parts
Once the components had been finished and configured, they were entered into Porsche’s standard ‘pulsation’ tests to check the thickness of their walls. The parts were also subjected to a ‘tear off’ examination, which ensured its pinball didn’t sheer under load. Not only did the 3D printed pistons pass, but they will now go on to further bench evaluations, which are designed to measure their longer-term endurance. These trials consist of 135 hours operating under full load, and 25 hours under drag load at a variety of speeds, in order to test its consistency.
“The results are in, and all the pistons passed the tests. Next, it’s on to the bench test, a 200-hour endurance test under the toughest conditions,” added Ulrich Kunzmann, Head of Prototype Manufacturing at MAHLE. “The positive results confirm the great potential of 3D printing, especially for high-performance, small and limited runs, and when it comes to prototyping.”
While testing remains ongoing, Porsche has not yet committed to fitting the 3D printed parts into its commercial vehicles. Nonetheless, the company did indicate that it had played it safe with the piston’s design, and the part could yet be further optimized to yield increased performance gains. “We’ve always made sure that we err on the safe side. Our simulations show that there is a potential weight saving of up to 20 percent per piston,” added Ickinger.
“The torsional vibration damper can then be made smaller, thereby making the engine even more free-revving. Increased thermal resistance due to the lower temperature also permits higher combustion pressures and even more advanced ignition timing — both factors that increase power and efficiency.”
As a result, 3D printing remains an important part of the company’s roadmap moving forwards, and it is excited about the potential of the technology within the industry. “I am certain that additive manufacturing will be an established part of automotive development and production,” concluded Ickinger. “In 10 years’ time at the latest.”

Additive manufacturing in the automotive industry
While Porsche hasn’t pledged to use its newly-developed pistons within its production cars, it has 3D printed a range of components for end-use applications in the past. In February 2018 for instance, the supercar manufacturer began printing spare parts for its rare and classic cars. This was followed by an announcement earlier this year, that it would be 3D printing personalized bucket seats for 40 prototypes to be used on European race tracks.
Other automotive companies have also reaped the benefits of additive manufacturing, such as the start-up Czinger, which is set to launch its first 3D printed hypercar, the 21C, in 2021. Using 3D printing, the $1.7M car will make weight and cost gains compared to traditional production methods, as well as benefiting from a reduction in manufacturing times.
Additive manufacturing consultancy firm APWORKS meanwhile, has 3D printed a metal part for the latest Bugatti Chiron hypercar. The exhaust tailpipe component was produced in titanium in order to make it more lightweight and temperature resistant.
You can now nominate for the 2020 3D Printing Industry Awards. Cast your vote to help decide this year’s winners.
To stay up to date with the latest 3D printing news, don’t forget to subscribe to the 3D Printing Industry newsletter or follow us on Twitter or liking our page on Facebook.
Looking for a job in the additive manufacturing industry? Visit 3D Printing Jobs for a selection of roles in the industry.
Featured image shows the 3D printed pistons that were developed in a collaborative effort by Porsche, TRUMPF, and MAHLE. Photo via Porsche.