We can all play a part in saving the planet from adverse climate change. From small efforts like recycling, reusing and minimizing waste and energy usage to developing new technologies and products to make an even bigger impact on climate change. For the last 25 years, I’ve been lucky enough to do both — I’ve been able to help make electric vehicle technology viable and bring many exciting electric vehicles into production. The instant torque and acceleration you feel in an EV is an addicting thrill and will undoubtedly put a smile on your face. Upon deceleration, you won’t quite get the same thrill but you can feel good about that as well because you’re putting energy back into the battery and not wasting it with friction, creating heat, like a normal ICE (Internal Combustion Engine) car when you hit the brakes.
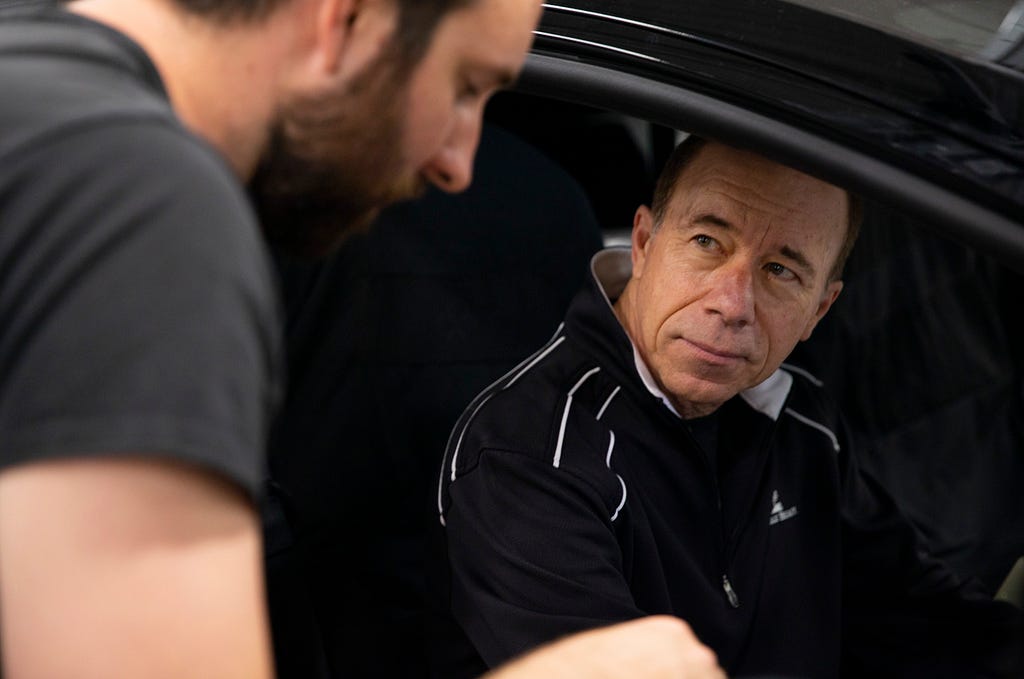
Speaking of exciting, we’ve been working on the next generation of EVs at Faraday. In fact, the FF 91 is really a new species of EV. Since I’m responsible for the propulsion system at Faraday, I wanted to share some information on it. The Faraday propulsion system is an extremely powerful and efficient modular system that can support different customer needs. The motor drive units can be used in one, two and three motor configurations while our high energy battery strings can be combined in any number that the customer and vehicle specs require.
We put a lot of skill, art and science into the development and integration of these new propulsion systems. The art part was in taking a clean sheet of paper approach in designing it as a fully integrated system that would not only be compact, but modular and easy to package into the vehicle as well.
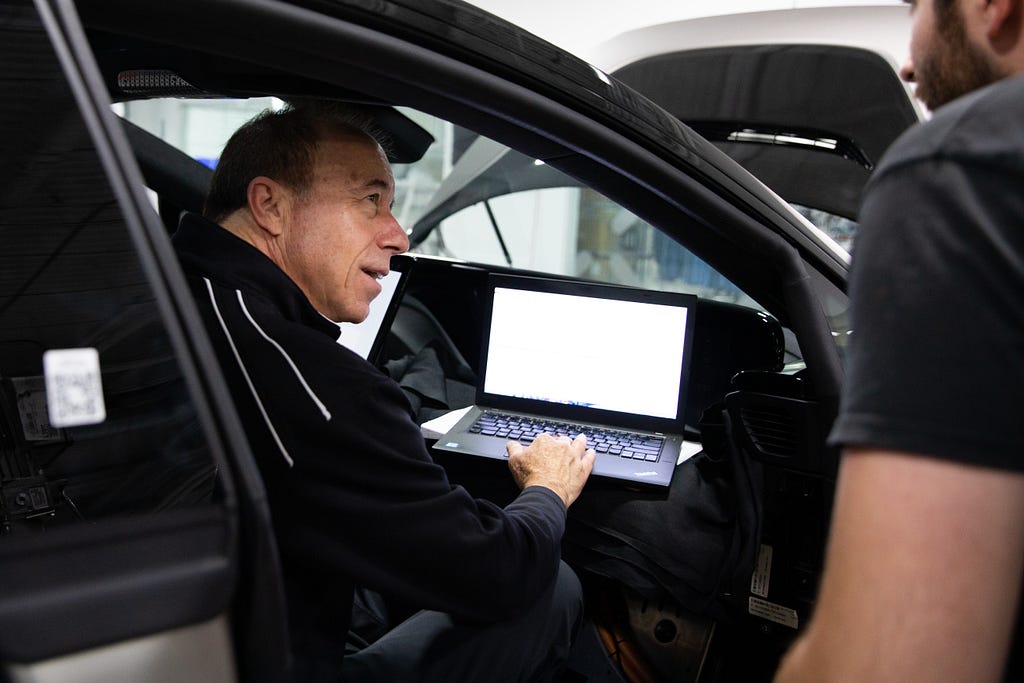
How does this all work together? The motor, gearbox and inverter form a totally integrated drive unit where heat is removed most efficiently by an oil spray that cools the stator-end turns instead of just containing the motor in a water jacket. The high-power inverter is mounted directly on the motor instead of using AC cables and connectors that are heavy, costly and difficult to package in a vehicle. The gearbox is a coaxial design that is more compact than an offset gearbox. The coaxial gearbox has an integrated park-pawl system for use on the front axle and two motors with two gearboxes that are used on the rear axle to provide torque vectoring for superior vehicle dynamics.
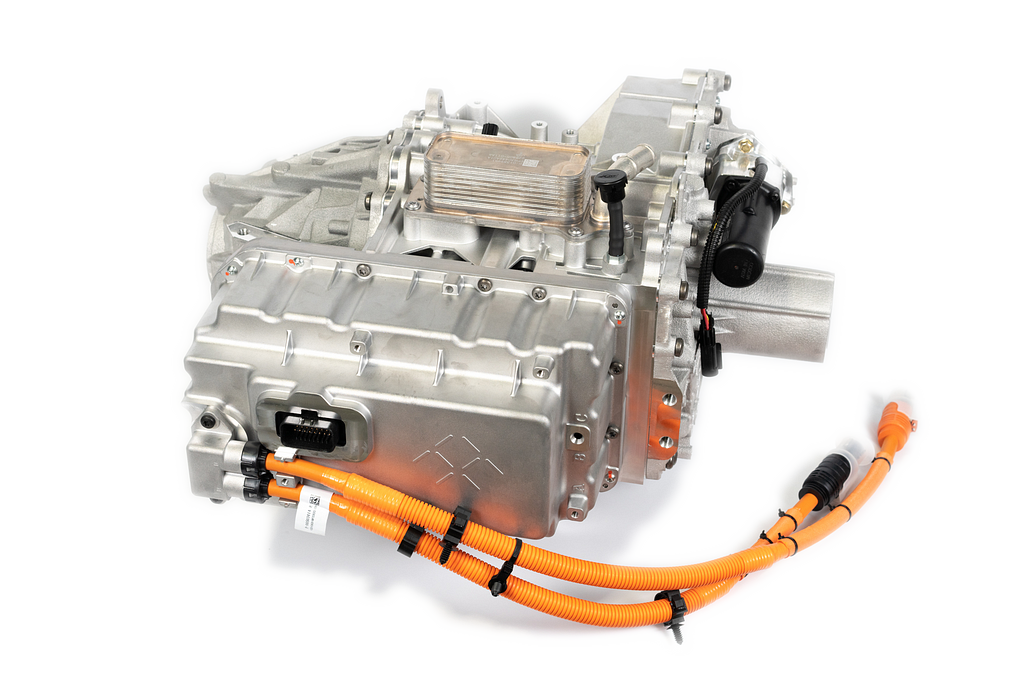
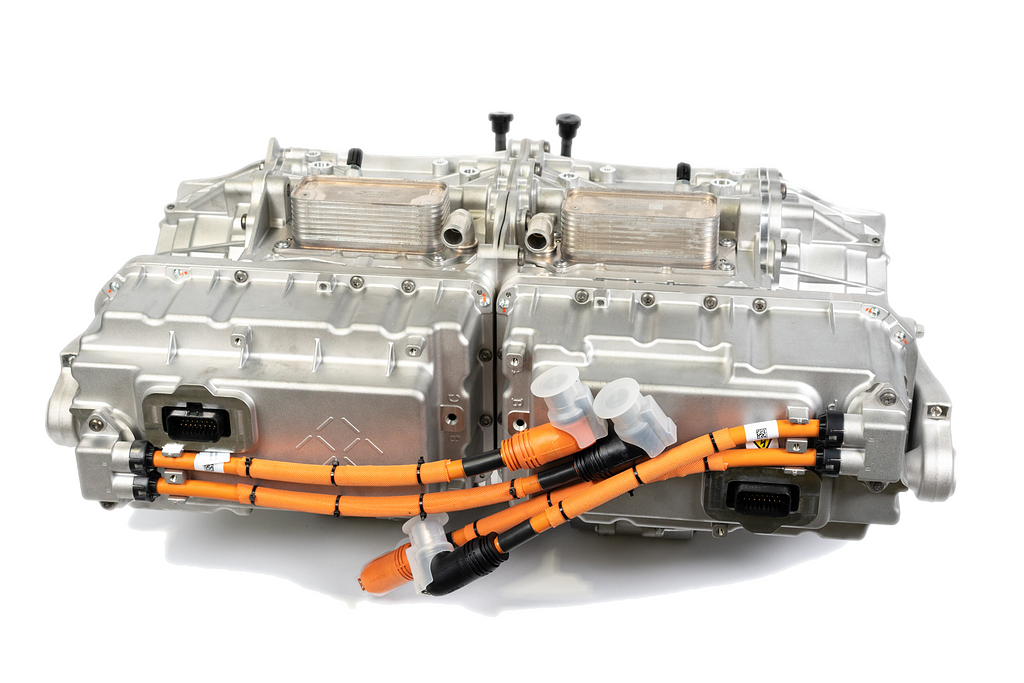
More of our clean-sheet paper approach was applied in the design of a modular high energy battery pack consisting of independent battery strings. Each battery string has its own built-in contactor, current sensor and fuse circuitry so that any number of battery strings can be used depending on vehicle range and packaging requirements. In the case of the FF 91, six strings are used but other vehicles could have a larger or smaller number of strings.
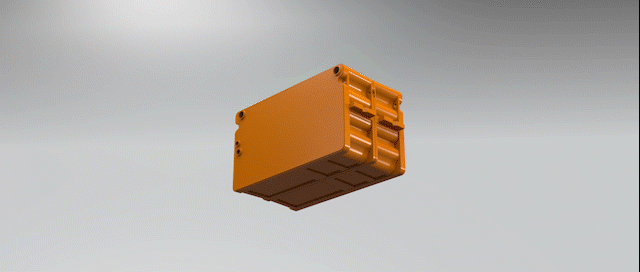
The science part came in during the design, development and integration of the drive units and battery packs packaged into the vehicle. Numerous electrical and Computational Fluid Dynamics (CFD) mechanical analyses were performed to optimize the design. The propulsion system has gone through several design iterations with laboratory and vehicle testing to ensure system performance requirements are met. Bringing this propulsion system that balances skill, art and science into production is the next step for us at Faraday. We can’t wait to bring it to the market and see how it makes our customers not only smile but also improves the world in which we live.
About the Author
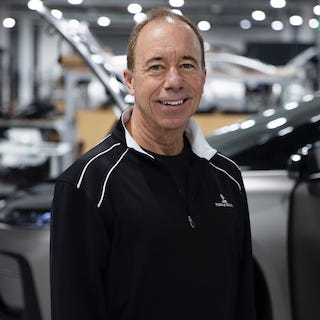
Mark Selogie is FF’s Senior Director of Propulsion and Electrical Engineering. His responsibilities include hardware and software development, integration and validation of Powertrain, Energy Storage & Charging, Thermal and Electrical components and systems. He has a Master’s degree in Electrical Engineering, holds 16 patents and has filed 11 invention disclosures at FF.