Top Engineering (CEO Seok-hyun Bang), a company specializing in automation facilities and inspection equipment in the secondary battery sector, announced on the 12th that it has developed the world’s first equipment to inspect and detect welding defects in the battery cell modular process.
This equipment inspects welding conditions in real-time through a monitoring system that applies sensing technology and its analysis algorithm and detects foreign substances such as dust. It is expected that it will be able to replace vision inspection equipment and manual welding inspection of workers, which are mainly used by the industry.
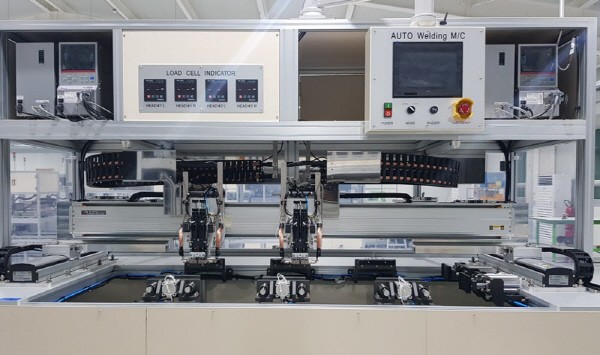
Since the existing vision inspection equipment inspects the welding status of the junction between the electrode tab and the cell through a camera mounted on the top of the welding machine, it was difficult to inspect the side, so separate manual work was required.
However, Top Engineering ‘s inspection and detection equipment not only inspects welding quality but also selects various foreign substances such as oil and dust at the junction of the cell and module before and after welding.
This is a monitoring technology that applies laser displacement sensors and analysis algorithms that measure fine distances and can detect excessive welding, weak welding conditions below standards, and degree of protrusion and even data.
If data obtained through the equipment is linked with the manufacturing execution system (MES), systematic quality control of the overall battery module process is possible. The company explains that it can fundamentally prevent degradation such as balancing problems that occur when charging and discharging batteries due to poor welding or capacity degradation.
Top Engineering has recently completed patent registration for inspection equipment for cylindrical battery resistance welding in Korea and is applying for overseas patents.
Top Engineering CEO Seok-hyun Bang said, “The current vision inspection equipment has been additionally inspected by workers using ceramic tweezers for accurate quality inspection, but the use of top equipment can significantly reduce working time as well as accuracy.” “This equipment has been supplied to Company I, a battery pack company, and has been using it for three months in actual mass production lines,” he said.
The inspection and detection equipment developed by Top Engineering this time is optimized for resistance welding, a process of modularizing cylindrical battery cells, and the company plans to release inspection and detection equipment optimized for laser welding processes in the future.
By Staff Reporter Tae-jun Park (gaius@etnews.com)