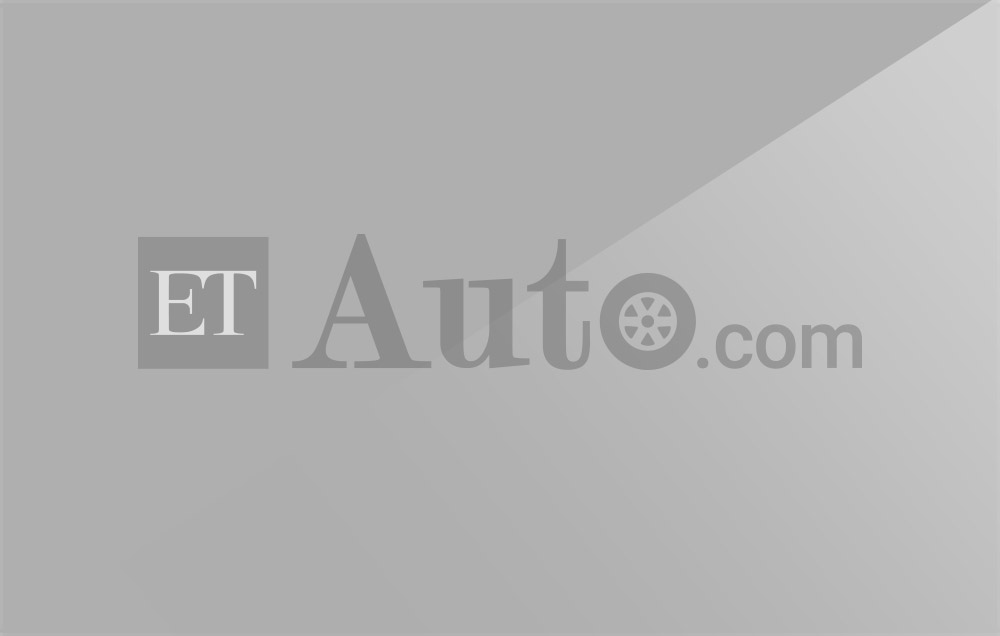
New Delhi: In an exclusive interaction with ETEnergyWorld, Hetal Gandhi, director, CRISIL Research, talks to us about the intricacies of the green hydrogen market, latest technologies at work, her expectations from the yet to be released second phase of the hydrogen policy, and much more. Edited excerpts:
Do you think India has announced investment plans which are too big for a technology which is still under research? Is the government and the industry rushing with their plans?
Major economies have fast-tracked their transition from conventional fuels to reduce emissions and to insulate themselves from the volatility of oil and gas prices. As a country that imports over 80 per cent and 55 per cent of its oil and gas requirements, respectively, India needs to follow suit.
Globally, investments in this space have so far exceeded $500 billion and electrolyser capacity is set to grow about 50 times to 15 GW by 2025, supported by favourable regulatory policies. India is favourably placed to manufacture green hydrogen and reduce oil and gas imports as it boasts of one of the most competitive RE tariffs.
Cheap solar PV cells are also key to reduce green hydrogen production costs. How big a challenge will it be for India in the coming years, given the fact that a major chunk of cells and modules continue to be imported from China and will be so for some more years too?
While the installed base for cells is a minimal 3 GW and for modules about 14 GW as of March 2022, policy support over the past two fiscal years lead us to expect a rapid expansion on this front.
According to our analysis, we expect an incremental 20-25 GW and 30-35 GW capacity being added by cell and module makers, respectively, through fiscal 2025. This will be sufficient to meet domestic demand, though technology and quality preferences will remain monitorables. Consequently, with backward integration established under PLI for 10-15 GW, coupled with increased supply, prices of domestic modules and cells should moderate over the period, aiding in affordable and sufficient availability.
Do we currently know which electrolyser technology is the most economical and secure?
Alkaline electrolyser (AE) technology is probably the most established and cheapest – it can be set up at just $700-800 per kW. Additionally, it has a high efficiency of about 75 per cent and a longer lifespan. However, a major disadvantage is its inability to adapt to variable power sources, as is the case with renewables. Also, AE systems need huge areas for deployment.
Proton exchange membrane (PEM) technology, on the other hand, addresses all the disadvantages of AE. However, it is not without demerits: Higher capital expenditure of $900-1,100 per kW, use of scarce and precious materials such as iridium and platinum, leading to cost of production being 20-25 per cent higher than for AE, to name some.
India largely uses AE, although GAIL recently made an announcement on deployment of PEM electrolyser. Globally, both technologies are being used. AE and PEM are at various stages of commercial launch, while solid oxide and anion exchange membrane are still at the proof of concept stage.
What are the safety, economic, and environment risks associated with green hydrogen?
Safety risks are the most critical for green hydrogen as it liquefies at -253 degree Celsius, which is difficult to achieve at an industrial level. Hence, for now, hydrogen production and transport will continue to be in gaseous form. Since gaseous hydrogen is colourless, odourless and burns with a nearly invisible flame, its leakage cannot be easily detected. Furthermore, the key risk lies in its high flammability in air or oxygen. Adequate ventilation and leak detection are important elements in the design of safe hydrogen systems.
In addition, some metals can become brittle when exposed to hydrogen, so selecting appropriate materials is also key to the design of hydrogen systems such as piping, containers, etc. The current natural gas pipelines in the country support only hydrogen blending and are not suitable for its transport in its pure form.
Economic risks would most likely arise from the industry’s inability to lower the cost of production. Also, there are demand-side risks involving lack of offtake of hydrogen from potential end-use sectors such as steel and transport, linked to the economic price and transition to new manufacturing technologies. Also, the cost of transportation through pipelines is quite high at $0.1-0.4 per kg for 50 km and needs to be trimmed to lower the supply cost of hydrogen.
Production of green hydrogen involves minimal environmental risk. There is, however, some environmental impact as the raw materials used in both the processes are metal, which are mined.
Where does India stand in the global green hydrogen landscape?
With capacity expansion of 85-90 GW over the past 10 years, RE tariffs are down from Rs 12 per unit to less than Rs 2 per unit – one of the most competitive globally. The possibilities are enormous.
In 2021, industrial CO2 emission in India was about 790 million tonnes, of which 70 per cent was from the steel, cement, aluminium, chemicals, refining and fertiliser sectors collectively. This can be substantially reduced by using green hydrogen. Foreign majors such as Stiesdal, Green Stat and Fortescue Future have also announced tie-ups with Indian players to catalyse hydrogen-based green transition.
What are your expectations from the second phase of the National Hydrogen Policy? What more needs to be done?
The second phase of the policy is likely to offer incentive schemes akin to PLI for electrolyser production. But a lot more needs to be done, such as state-level incentives on open access charges for transporting renewables. This, combined with a strengthened system on trading RE certificates and a fast evolving C&I market, will play a critical role. The demand side needs to be addressed, too. Mandatory green hydrogen targets should be set up across key end-use sectors such as fertilisers and steel to ensure offtake.