When space is at a premium and you need to charge multiple vehicles at high power, you might be required to build chargers upstairs
Together with launch of series production of electric buses, Daimler retrofitted its Mannheim bus plant in Germany with a new central electric charging station for Mercedes-Benz eCitaro.
It’s quite interesting to look at the approach to implement electrification. In the case of the Mannheim plant, there is a 1.2 MW station with four 150 kW DC CCS Combo 2 stalls plus two different overhead charging systems (300 kW each) for two stands.
The newly produced eCitaro can be now fast charged and tested ahead of customer delivery. Additionally, the station will be used for the development of new products as well as for presentation to customers.
Interesting thing is that all the chargers are installed around five meters above the ground to save space at the facility.
Similar stations might be the way to go also for many bus depots, limited by space.
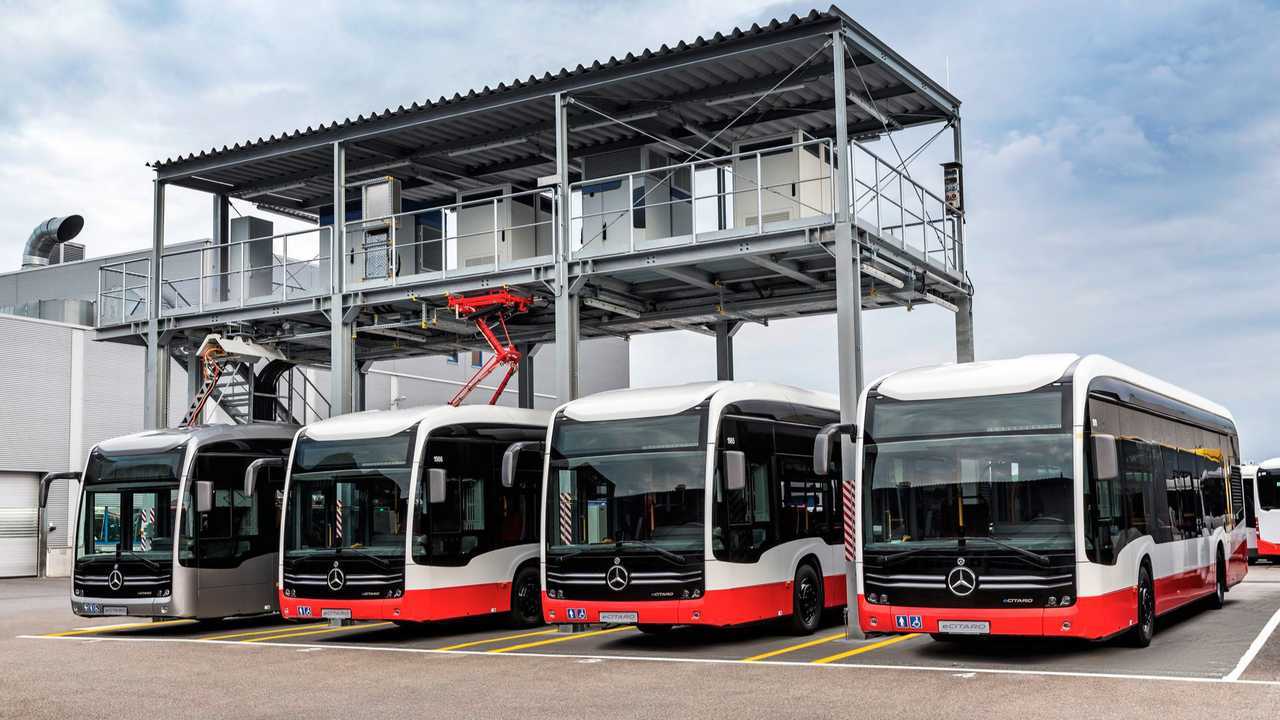
Flexible and modular infrastructure concept for the relevant charging solutions: charging via cable, pantograph and charging rail
The charging station is compatible with all common charging technologies: 150 kW cable-bound charging, 300 kW rapid charging using a pantograph on the bus roof and 300 kW rapid charging using a permanently installed set of charging rails on the roof of the bus. In technical jargon, the latter is referred to as an inverted pantograph.
All four parking bays are setup to handle the particularly common cable-bound charging of the eCitaro. And in line with this, it can handle the different charging systems of two manufacturers. Using them, buses can be charged with an output of 150 kW. Two parking bays additionally offer rapid charging via the vehicle roof; one uses a pantograph, the other uses charging rails. In both cases, the charging output is 300 kW. The entire system has a modular design to ensure that it can be expanded as required.
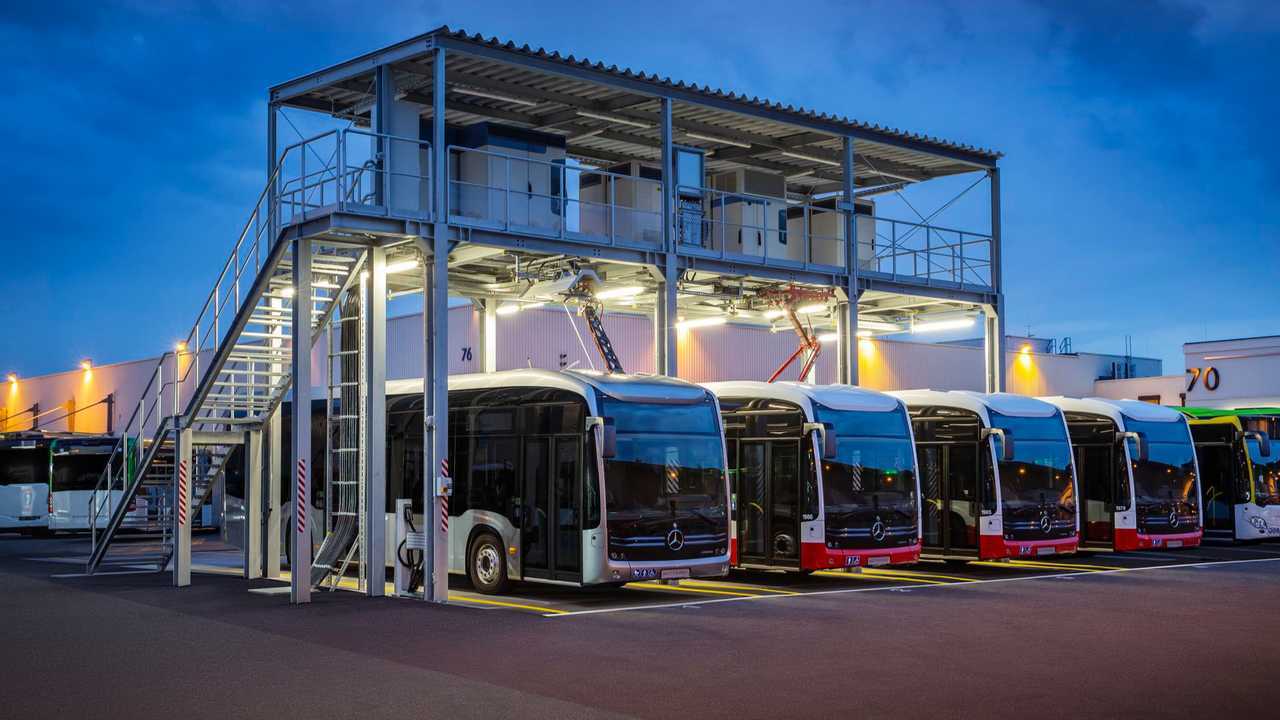
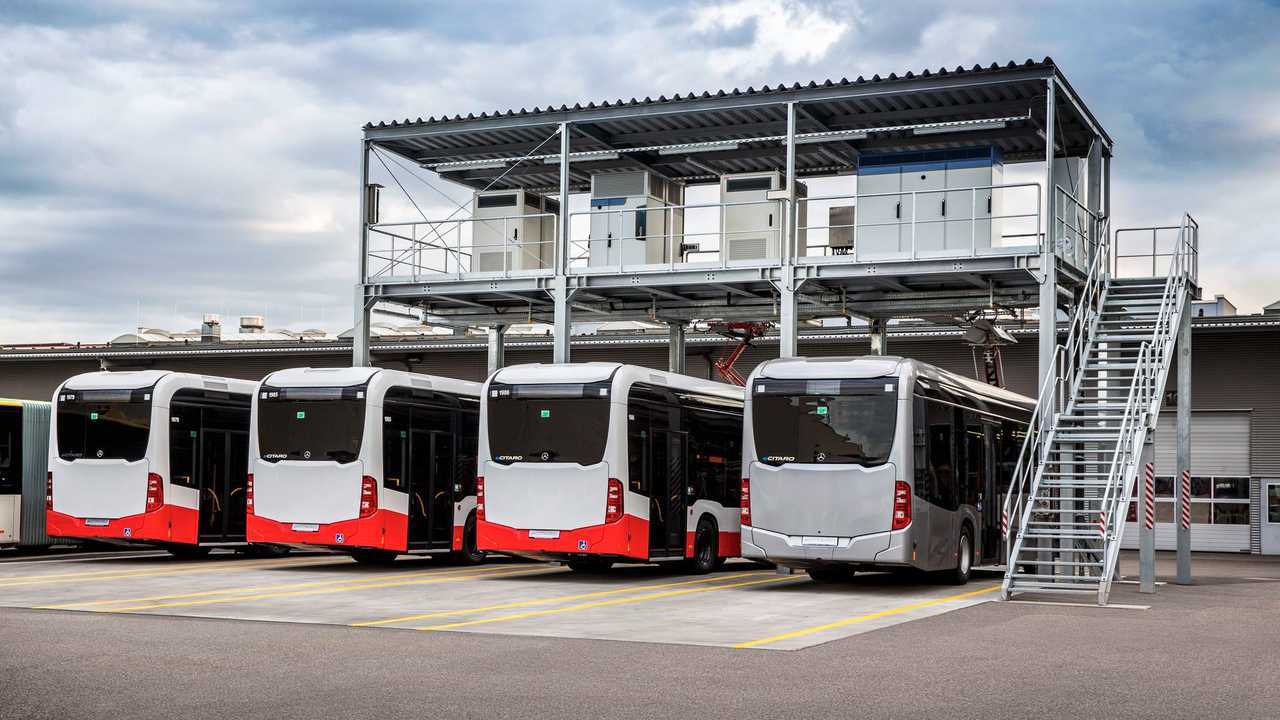
The next step for e-mobility at Daimler Buses
- Flexible and modular infrastructure concept for the relevant charging solutions: charging via cable, pantograph and charging rail
- New central electric charging station for the Mercedes-Benz eCitaro at the Mannheim bus plant
- Central point of call for charging during the production process, as well as for testing and further development, as well as for charging prior to delivery
- Information about charging technologies for customers
Stuttgart / Mannheim – Preparing for the market launch of high-output charging, Daimler Buses has equipped its Mannheim bus plant with a central charging station for the fully-electric eCitaro. It can also be used to provide the newly released eCitaro with electricity via a pantograph. The special feature of this charging station is that the charging devices are suspended at a height of around five metres above the ground. The station serves to charge the eCitaro as part of the production process and ahead of delivery to customers. Plus, new charging technologies such as charging management, new communications protocols, new hardware for charging using a cable or a roof-mounted pantograph can be tried and tested. What’s more, the infrastructure is expandable as required.
Flexible and modular infrastructure concept for the relevant charging solutions: charging via cable, pantograph and charging rail
The charging station is compatible with all common charging technologies: 150 kW cable-bound charging, 300 kW rapid charging using a pantograph on the bus roof and 300 kW rapid charging using a permanently installed set of charging rails on the roof of the bus. In technical jargon, the latter is referred to as an inverted pantograph.
All four parking bays are setup to handle the particularly common cable-bound charging of the eCitaro. And in line with this, it can handle the different charging systems of two manufacturers. Using them, buses can be charged with an output of 150 kW. Two parking bays additionally offer rapid charging via the vehicle roof; one uses a pantograph, the other uses charging rails. In both cases, the charging output is 300 kW. The entire system has a modular design to ensure that it can be expanded as required.
New central electric charging station for the Mercedes-Benz eCitaro at the Mannheim bus plant
As space in the bus plant is at a premium, Mercedes-Benz has decided to move off the ground, installing the eCitaro charging station at the height of the upper floor of the building. An idea which many transport companies also use. It doesn’t just save space, it also protects against costly accidents between manoeuvring buses and the charging technology.
The electric charging station is located directly behind the vehicle handover hall and thus has a strategically interesting location. To save electrically-powered city buses from having to carry out complex manoeuvring, the charging station has been built in a space-saving way to resemble a bridge. The city buses drive straight under the charging station and park right there for charging.
The charging station has four parking bays. It uses four charging devices with 150 kW output each and two with 300 kW each. The six charging devices enjoy shared use by three different technologies and two different manufacturers. The total connection power at the charging station is an impressive 1.2 megawatts. The corresponding cables are roughly as thick as a human arm and run in an extendible cable channel in the ground.
The charging station is positioned on a total of ten pillars and is accessible from all sides. For service purposes, wide steps lead up to the charging devices on the upper deck, as it were. These are protected against the influences of the weather by means of a roof.
Charging before delivery and for test purposes, as well as an information station for customers
There were several reasons which led to the decision to set up the central electric charging station within the plant’s premises. After leaving the production line, each new eCitaro is put through a comprehensive series of tests, both at the company’s own test track and on public roads – and the pre-requisite for completing this intense series of checks, which are incidentally also part of the regular Citaro’s production process, is of course a charged battery. At the charging station, the focus is on testing both charging via the roof and the vehicle’s own technology. The checks for road approval-relevant aspects already take place before the test drives. Also charged here ahead of their company-internal test drives are test vehicles and new technologies. Lastly, customers visiting the plant can also stop by at the electric charging station and read the information panels there regarding the various charging technologies as well as seeing them in use first-hand.